Calibração RBC: Como Garantir Precisão e Confiabilidade em Seus Equipamentos
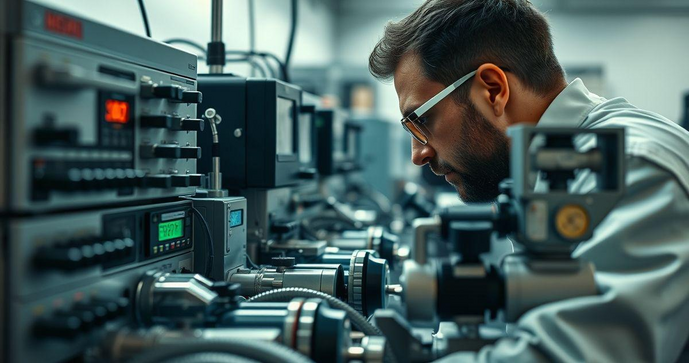
Por: Rafael - 21 de Fevereiro de 2025
A Calibração RBC é um processo fundamental para garantir a precisão e a confiabilidade de equipamentos em diversas indústrias. Com a crescente demanda por resultados exatos, entender como realizar a calibração de forma adequada se torna essencial. Neste artigo, abordaremos a importância da Calibração RBC, os passos necessários para executá-la corretamente e os erros comuns que devem ser evitados, além de discutir a frequência recomendada para esse procedimento. Prepare-se para otimizar o desempenho dos seus equipamentos e assegurar resultados confiáveis.
Importância da Calibração RBC para Equipamentos Precisos
A calibração RBC (Referência de Calibração de Balança) é um procedimento essencial que garante a precisão e a confiabilidade dos equipamentos utilizados em diversas indústrias. A precisão das medições é crucial em setores como farmacêutico, alimentício, químico e de engenharia, onde pequenas variações podem resultar em consequências significativas. Neste contexto, a calibração adequada se torna uma prática indispensável para assegurar que os equipamentos estejam funcionando dentro dos padrões estabelecidos.
Um dos principais motivos para a realização da calibração RBC é a necessidade de conformidade com normas e regulamentos. Muitas indústrias são obrigadas a seguir diretrizes específicas que exigem a calibração regular de seus equipamentos. Isso não apenas garante a qualidade dos produtos, mas também protege a empresa de possíveis penalidades legais. Além disso, a calibração ajuda a manter a reputação da empresa, demonstrando um compromisso com a qualidade e a segurança.
Outro aspecto importante da calibração RBC é a redução de erros de medição. Equipamentos que não são calibrados regularmente podem apresentar desvios que afetam a precisão das medições. Esses desvios podem ser causados por diversos fatores, como desgaste, variações de temperatura, umidade e até mesmo interferências eletromagnéticas. Ao realizar a calibração, é possível identificar e corrigir esses erros, garantindo que os resultados obtidos sejam confiáveis e representativos.
A calibração também desempenha um papel fundamental na otimização de processos. Em ambientes industriais, a eficiência é uma prioridade. Equipamentos que operam com medições imprecisas podem levar a desperdícios de materiais, retrabalhos e até mesmo falhas na produção. Ao garantir que os equipamentos estejam calibrados corretamente, as empresas podem melhorar a eficiência operacional, reduzindo custos e aumentando a produtividade.
Além disso, a calibração RBC é vital para a segurança dos trabalhadores e do ambiente. Em indústrias onde substâncias químicas perigosas são manipuladas, por exemplo, medições imprecisas podem resultar em acidentes graves. A calibração regular dos equipamentos garante que as medições estejam dentro dos limites seguros, protegendo não apenas os trabalhadores, mas também o meio ambiente. A segurança deve ser sempre uma prioridade, e a calibração é uma ferramenta essencial para alcançá-la.
Outro ponto a ser considerado é a importância da calibração na manutenção da integridade dos dados. Em muitas indústrias, os dados coletados são utilizados para análises e tomadas de decisão. Se os dados forem imprecisos devido a medições erradas, as decisões tomadas com base nesses dados podem ser comprometidas. A calibração ajuda a garantir que os dados sejam precisos e confiáveis, permitindo que as empresas tomem decisões informadas e estratégicas.
Um exemplo prático da importância da calibração RBC pode ser observado no uso de Medidor de vazão ultrassônico. Este equipamento é amplamente utilizado para medir a vazão de líquidos em diversas aplicações. Se o medidor não estiver calibrado corretamente, as medições de vazão podem estar erradas, resultando em problemas como o desperdício de recursos ou a incapacidade de atender a requisitos de produção. Portanto, a calibração regular desse tipo de equipamento é crucial para garantir que as medições sejam precisas e que os processos operacionais sejam eficientes.
Além disso, a calibração RBC contribui para a longevidade dos equipamentos. Equipamentos que não são calibrados regularmente podem sofrer desgastes mais rapidamente, resultando em custos elevados de manutenção e substituição. Ao realizar a calibração, é possível identificar problemas antes que se tornem críticos, permitindo que as empresas realizem manutenções preventivas e prolonguem a vida útil dos equipamentos.
Por fim, a calibração RBC é uma prática que promove a cultura da qualidade dentro das organizações. Ao estabelecer procedimentos de calibração e garantir que todos os colaboradores estejam cientes da importância desse processo, as empresas criam um ambiente de trabalho que valoriza a precisão e a qualidade. Isso não apenas melhora a eficiência operacional, mas também contribui para a satisfação do cliente, que espera produtos e serviços de alta qualidade.
Em resumo, a calibração RBC é um componente essencial para garantir a precisão e a confiabilidade dos equipamentos utilizados em diversas indústrias. Desde a conformidade com normas até a otimização de processos e a segurança dos trabalhadores, os benefícios da calibração são inegáveis. Investir em calibração regular é um passo fundamental para qualquer empresa que busca manter altos padrões de qualidade e eficiência em suas operações.
Passo a Passo para Realizar a Calibração RBC
Realizar a calibração RBC (Referência de Calibração de Balança) é um processo fundamental para garantir a precisão e a confiabilidade dos equipamentos utilizados em diversas indústrias. A calibração adequada não apenas assegura que os instrumentos estejam funcionando corretamente, mas também ajuda a manter a conformidade com normas e regulamentos. A seguir, apresentamos um passo a passo detalhado para realizar a calibração RBC de forma eficaz.
1. Preparação e Planejamento
Antes de iniciar o processo de calibração, é essencial realizar um planejamento adequado. Isso inclui a definição dos equipamentos que serão calibrados, a frequência da calibração e a identificação dos padrões de referência que serão utilizados. É importante também verificar se todos os instrumentos necessários para a calibração estão disponíveis e em boas condições de uso.
Além disso, é recomendável consultar as Empresas de calibração de equipamentos que podem fornecer suporte técnico e orientação sobre os procedimentos corretos a serem seguidos. Essas empresas possuem experiência e conhecimento que podem ser valiosos durante o processo de calibração.
2. Verificação do Equipamento
Antes de iniciar a calibração, é fundamental realizar uma verificação inicial do equipamento. Isso envolve a inspeção visual para identificar qualquer dano físico, desgaste ou sujeira que possa afetar a precisão das medições. Certifique-se de que o equipamento esteja limpo e livre de obstruções.
Além disso, verifique se o equipamento está em um ambiente adequado para a calibração. Fatores como temperatura, umidade e vibrações podem influenciar os resultados da calibração. Portanto, é importante garantir que o ambiente esteja controlado e que as condições sejam favoráveis para a realização do procedimento.
3. Seleção dos Padrões de Referência
A calibração deve ser realizada utilizando padrões de referência que sejam rastreáveis a padrões nacionais ou internacionais. Esses padrões são essenciais para garantir que as medições realizadas pelo equipamento calibrado sejam precisas e confiáveis. A escolha dos padrões deve ser feita com base nas especificações do equipamento e nas normas aplicáveis ao setor.
Os padrões de referência devem ser verificados quanto à sua precisão e validade. Certifique-se de que eles estejam dentro do período de validade e que tenham sido calibrados recentemente. Isso é crucial para garantir a confiabilidade dos resultados obtidos durante a calibração.
4. Realização da Calibração
Com todos os preparativos concluídos, é hora de realizar a calibração. O processo pode variar dependendo do tipo de equipamento, mas geralmente envolve a aplicação de pesos ou padrões de referência conhecidos e a comparação das medições obtidas com os valores esperados.
Durante a calibração, é importante seguir as instruções do fabricante do equipamento e as normas aplicáveis. Registre todas as medições e resultados obtidos, pois esses dados serão essenciais para a análise posterior e para a documentação da calibração.
Se o equipamento apresentar desvios em relação aos padrões de referência, ajustes devem ser feitos. Isso pode incluir a reconfiguração do equipamento ou a realização de ajustes mecânicos. Após os ajustes, repita o processo de calibração para garantir que o equipamento esteja dentro das especificações desejadas.
5. Documentação dos Resultados
Após a conclusão da calibração, é fundamental documentar todos os resultados obtidos. Isso inclui a criação de um relatório de calibração que contenha informações sobre o equipamento, os padrões utilizados, as medições realizadas e quaisquer ajustes feitos durante o processo.
A documentação é essencial para garantir a rastreabilidade e a conformidade com as normas e regulamentos. Além disso, ela serve como um registro que pode ser consultado em auditorias e inspeções futuras.
6. Manutenção e Monitoramento Contínuo
A calibração não deve ser vista como um evento isolado, mas sim como parte de um processo contínuo de manutenção e monitoramento. É importante estabelecer um cronograma de calibração regular para garantir que os equipamentos permaneçam precisos ao longo do tempo.
Além disso, monitore o desempenho dos equipamentos após a calibração. Se houver sinais de desvios ou problemas, realize verificações adicionais e intervenções conforme necessário. A manutenção preventiva é fundamental para evitar falhas e garantir a confiabilidade dos equipamentos.
7. Treinamento e Capacitação
Por fim, é importante garantir que a equipe responsável pela calibração esteja devidamente treinada e capacitada. O conhecimento sobre os procedimentos corretos, os padrões de referência e as normas aplicáveis é essencial para a realização de calibrações eficazes.
Investir em treinamento contínuo e atualização sobre as melhores práticas de calibração pode resultar em melhorias significativas na precisão e na confiabilidade dos equipamentos. Isso, por sua vez, contribui para a qualidade dos produtos e serviços oferecidos pela empresa.
Em resumo, a calibração RBC é um processo que requer planejamento, atenção aos detalhes e um compromisso com a qualidade. Seguir este passo a passo garantirá que os equipamentos estejam sempre funcionando de maneira precisa e confiável, contribuindo para a eficiência operacional e a conformidade com as normas do setor.
Erros Comuns na Calibração RBC e Como Evitá-los
A calibração RBC (Referência de Calibração de Balança) é um processo crítico para garantir a precisão e a confiabilidade dos equipamentos utilizados em diversas indústrias. No entanto, existem erros comuns que podem comprometer a eficácia da calibração e levar a resultados imprecisos. Neste artigo, abordaremos os principais erros cometidos durante a calibração RBC e forneceremos dicas sobre como evitá-los.
1. Falta de Planejamento Adequado
Um dos erros mais frequentes na calibração é a falta de planejamento adequado. Muitas vezes, as empresas realizam a calibração de forma apressada, sem definir claramente os objetivos, os padrões de referência e os procedimentos a serem seguidos. Isso pode resultar em medições imprecisas e na necessidade de recalibrações frequentes.
Para evitar esse erro, é fundamental elaborar um plano de calibração detalhado. Isso deve incluir a definição dos equipamentos a serem calibrados, a frequência da calibração e a escolha dos padrões de referência. Um planejamento cuidadoso ajuda a garantir que todos os aspectos da calibração sejam considerados e que o processo seja realizado de forma eficiente.
2. Ignorar as Condições Ambientais
As condições ambientais podem ter um impacto significativo na precisão das medições. Fatores como temperatura, umidade e vibrações podem afetar o desempenho dos equipamentos durante a calibração. Ignorar essas condições pode levar a resultados imprecisos e a falhas na calibração.
Para evitar esse erro, é importante realizar a calibração em um ambiente controlado. Certifique-se de que a temperatura e a umidade estejam dentro dos limites recomendados pelo fabricante do equipamento. Além disso, minimize as vibrações e outras interferências que possam afetar as medições. Um ambiente adequado é essencial para garantir a precisão dos resultados.
3. Uso de Padrões de Referência Inadequados
Outro erro comum é o uso de padrões de referência inadequados ou não rastreáveis. A calibração deve ser realizada utilizando padrões que sejam rastreáveis a padrões nacionais ou internacionais. O uso de padrões não confiáveis pode comprometer a precisão das medições e levar a resultados errôneos.
Para evitar esse problema, sempre verifique a validade e a rastreabilidade dos padrões de referência utilizados na calibração. Certifique-se de que eles estejam dentro do período de validade e que tenham sido calibrados recentemente. Isso garantirá que as medições realizadas sejam precisas e confiáveis.
4. Falta de Documentação Adequada
A documentação é uma parte crucial do processo de calibração. A falta de registros adequados pode levar a problemas de rastreabilidade e conformidade. Muitas empresas cometem o erro de não documentar os resultados da calibração, os padrões utilizados e quaisquer ajustes feitos durante o processo.
Para evitar esse erro, é fundamental criar um relatório de calibração detalhado que contenha todas as informações relevantes. Isso inclui dados sobre o equipamento, os padrões utilizados, as medições realizadas e quaisquer ajustes feitos. A documentação adequada não apenas ajuda a garantir a conformidade, mas também serve como um registro valioso para auditorias e inspeções futuras.
5. Negligenciar a Manutenção dos Equipamentos
A calibração não deve ser vista como um evento isolado, mas sim como parte de um processo contínuo de manutenção. Negligenciar a manutenção dos equipamentos pode levar a falhas e a medições imprecisas. Muitas empresas realizam a calibração, mas não investem na manutenção regular dos equipamentos, o que pode comprometer a eficácia da calibração.
Para evitar esse erro, é importante estabelecer um cronograma de manutenção regular para os equipamentos. Isso deve incluir inspeções periódicas, limpeza e lubrificação, conforme necessário. A manutenção preventiva ajuda a garantir que os equipamentos permaneçam em boas condições e que as medições sejam precisas ao longo do tempo.
6. Falta de Treinamento da Equipe
A calibração é um processo técnico que requer conhecimento e habilidades específicas. A falta de treinamento adequado da equipe responsável pela calibração pode resultar em erros e medições imprecisas. Muitas empresas cometem o erro de não investir em treinamento contínuo para seus colaboradores.
Para evitar esse problema, é fundamental garantir que a equipe responsável pela calibração esteja devidamente treinada e capacitada. Isso inclui o conhecimento sobre os procedimentos corretos, os padrões de referência e as normas aplicáveis. Investir em treinamento contínuo pode resultar em melhorias significativas na precisão e na confiabilidade das calibrações realizadas.
7. Ignorar a Importância da Recalibração
Após a calibração, muitas empresas ignoram a importância da recalibração regular. A calibração não é um processo único; os equipamentos podem sofrer desgastes e variações ao longo do tempo, o que pode afetar a precisão das medições. Ignorar a necessidade de recalibração pode levar a resultados imprecisos e a problemas de qualidade.
Para evitar esse erro, é importante estabelecer um cronograma de recalibração regular com base nas recomendações do fabricante e nas normas do setor. A recalibração ajuda a garantir que os equipamentos permaneçam precisos e confiáveis ao longo do tempo, contribuindo para a qualidade dos produtos e serviços oferecidos pela empresa.
Um exemplo prático da importância da calibração pode ser observado no uso de Medidor de vazão. Se o medidor não estiver calibrado corretamente, as medições de vazão podem estar erradas, resultando em problemas como o desperdício de recursos ou a incapacidade de atender a requisitos de produção. Portanto, a calibração regular desse tipo de equipamento é crucial para garantir que as medições sejam precisas e que os processos operacionais sejam eficientes.
Em resumo, evitar erros comuns na calibração RBC é essencial para garantir a precisão e a confiabilidade dos equipamentos. Desde o planejamento adequado até a documentação e a manutenção, cada etapa do processo de calibração deve ser realizada com atenção e cuidado. Ao seguir as melhores práticas e investir em treinamento e manutenção, as empresas podem melhorar a eficácia de suas calibrações e garantir a qualidade de seus produtos e serviços.
Frequência Recomendada para a Calibração RBC
A calibração RBC (Referência de Calibração de Balança) é um processo essencial para garantir a precisão e a confiabilidade dos equipamentos utilizados em diversas indústrias. No entanto, a eficácia da calibração não depende apenas da execução correta do procedimento, mas também da frequência com que ele é realizado. Neste artigo, discutiremos a frequência recomendada para a calibração RBC, fatores que influenciam essa frequência e a importância de manter um cronograma regular de calibração.
1. Importância da Frequência de Calibração
A calibração regular é fundamental para garantir que os equipamentos estejam funcionando dentro das especificações e que as medições sejam precisas. A falta de calibração pode resultar em desvios que afetam a qualidade dos produtos e serviços, além de comprometer a segurança em ambientes onde medições precisas são cruciais. Portanto, estabelecer uma frequência adequada para a calibração é essencial para manter a conformidade com normas e regulamentos, além de assegurar a qualidade e a segurança dos processos.
2. Fatores que Influenciam a Frequência de Calibração
Vários fatores podem influenciar a frequência recomendada para a calibração RBC. Entre eles, destacam-se:
- Tipo de Equipamento: Diferentes tipos de equipamentos têm diferentes requisitos de calibração. Equipamentos que operam em condições severas ou que são utilizados para medições críticas podem exigir calibrações mais frequentes.
- Intensidade de Uso: Equipamentos que são utilizados com frequência ou que passam por ciclos de operação intensos podem sofrer desgastes mais rapidamente, exigindo calibrações mais regulares.
- Condições Ambientais: Fatores como temperatura, umidade e vibrações podem afetar a precisão das medições. Equipamentos expostos a condições adversas podem precisar de calibrações mais frequentes.
- Normas e Regulamentações: Algumas indústrias são obrigadas a seguir normas específicas que determinam a frequência de calibração. É importante estar ciente dessas exigências para garantir a conformidade.
- Histórico de Desvios: Se um equipamento apresentar desvios frequentes durante as medições, pode ser necessário aumentar a frequência de calibração para garantir a precisão.
3. Recomendações Gerais de Frequência
Embora a frequência de calibração possa variar de acordo com os fatores mencionados, algumas recomendações gerais podem ser seguidas:
- Equipamentos Críticos: Para equipamentos que desempenham um papel crucial na segurança ou na qualidade do produto, como balanças de precisão em laboratórios, a calibração deve ser realizada pelo menos uma vez por mês.
- Equipamentos Moderadamente Críticos: Equipamentos que são utilizados em processos importantes, mas que não têm um impacto direto na segurança, podem ser calibrados a cada três a seis meses.
- Equipamentos de Uso Geral: Para equipamentos que são utilizados em condições normais e que não apresentam riscos significativos, a calibração pode ser realizada anualmente.
É importante ressaltar que essas são diretrizes gerais e que a frequência real de calibração deve ser ajustada com base nas necessidades específicas de cada equipamento e nas condições de operação.
4. Estabelecendo um Cronograma de Calibração
Para garantir que a calibração seja realizada de forma consistente, é recomendável estabelecer um cronograma de calibração. Isso pode incluir a criação de um calendário que indique as datas programadas para a calibração de cada equipamento, bem como a designação de responsáveis pela execução do procedimento.
Além disso, é importante documentar todas as calibrações realizadas, incluindo os resultados e quaisquer ajustes feitos. Essa documentação não apenas ajuda a manter a rastreabilidade, mas também fornece informações valiosas para futuras análises e auditorias.
Se a sua empresa não possui recursos internos para realizar a calibração, considere contratar uma Empresa de calibração de instrumentos de medição. Essas empresas possuem a experiência e o conhecimento necessários para garantir que a calibração seja realizada de acordo com as melhores práticas e normas do setor.
5. Monitoramento e Avaliação Contínua
Após estabelecer um cronograma de calibração, é importante monitorar e avaliar continuamente a eficácia do processo. Isso inclui a análise dos resultados das calibrações e a identificação de quaisquer tendências ou problemas que possam surgir. Se um equipamento apresentar desvios frequentes, pode ser necessário revisar a frequência de calibração e ajustar o cronograma conforme necessário.
Além disso, a realização de auditorias internas pode ajudar a garantir que os procedimentos de calibração estejam sendo seguidos corretamente e que os equipamentos estejam sendo mantidos em boas condições. Essas auditorias podem identificar áreas de melhoria e garantir que a empresa esteja em conformidade com as normas e regulamentos aplicáveis.
6. Conclusão
Em resumo, a frequência recomendada para a calibração RBC é um aspecto crucial para garantir a precisão e a confiabilidade dos equipamentos. Estabelecer um cronograma de calibração adequado, levando em consideração os fatores que influenciam a frequência, é essencial para manter a qualidade e a segurança dos processos. Ao seguir as melhores práticas e investir em calibração regular, as empresas podem melhorar a eficácia de suas operações e garantir a conformidade com as normas do setor.
Em conclusão, a Calibração RBC é um elemento crucial para a manutenção da precisão e confiabilidade dos equipamentos utilizados em diversas indústrias. Através da compreensão de sua importância, da execução correta dos passos necessários e da conscientização sobre os erros comuns a serem evitados, as empresas podem garantir que seus processos operacionais sejam eficientes e seguros. Além disso, estabelecer uma frequência adequada para a calibração é vital para assegurar que os equipamentos permaneçam dentro das especificações e que as medições sejam sempre precisas. Investir em calibração regular não apenas melhora a qualidade dos produtos e serviços, mas também contribui para a conformidade com normas e regulamentos, promovendo um ambiente de trabalho mais seguro e eficiente.