Calibração e Aferição de Instrumentos de Medição para Precisão e Confiabilidade
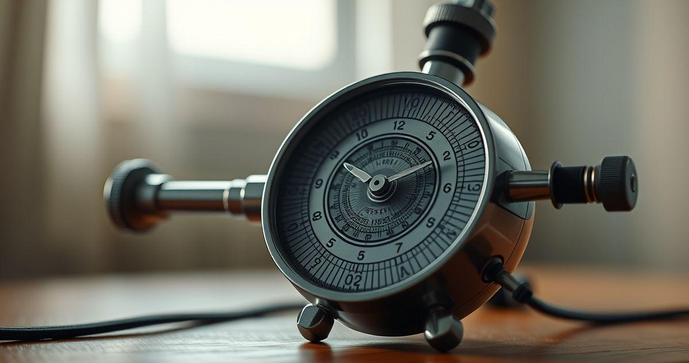
Por: Rafael - 22 de Fevereiro de 2025
A calibração e aferição de instrumentos de medição são processos fundamentais para garantir a precisão e a confiabilidade dos resultados em diversas aplicações industriais e laboratoriais. Esses procedimentos asseguram que os instrumentos estejam funcionando corretamente, evitando erros que podem comprometer a qualidade dos produtos e serviços. Neste artigo, abordaremos a importância da calibração e aferição, os métodos utilizados, a frequência recomendada e os erros comuns que devem ser evitados.
Importância da Calibração e Aferição na Indústria
A calibração e aferição de instrumentos de medição desempenham um papel crucial na indústria, garantindo que os processos produtivos sejam realizados com precisão e eficiência. Esses procedimentos são essenciais para manter a qualidade dos produtos, a segurança dos trabalhadores e a conformidade com as normas regulatórias. Neste contexto, a calibração refere-se ao ajuste de um instrumento de medição para que suas leituras correspondam a valores conhecidos, enquanto a aferição é o processo de verificação da precisão do instrumento em relação a padrões estabelecidos.
Um dos principais motivos para a calibração e aferição é a necessidade de garantir a qualidade do produto final. Em setores como a indústria alimentícia, farmacêutica e de manufatura, a precisão nas medições é vital. Por exemplo, em uma linha de produção de alimentos, a medição correta de ingredientes é fundamental para garantir que os produtos atendam aos padrões de qualidade e segurança. Se um instrumento de medição estiver descalibrado, isso pode resultar em produtos fora das especificações, levando a desperdícios, recalls e danos à reputação da empresa.
Além disso, a calibração e aferição são essenciais para a segurança operacional. Em indústrias que lidam com substâncias perigosas ou processos críticos, como a petroquímica, a precisão nas medições pode ser a diferença entre um ambiente seguro e um potencial desastre. Instrumentos de medição, como sensores de pressão e temperatura, devem ser calibrados regularmente para garantir que estejam funcionando corretamente e evitando situações de risco. A falta de calibração pode resultar em falhas de equipamentos, acidentes e até mesmo em perdas humanas.
Outro aspecto importante é a conformidade com normas e regulamentos. Muitas indústrias são obrigadas a seguir padrões específicos estabelecidos por órgãos reguladores, como a ISO (Organização Internacional de Normalização) e a ANVISA (Agência Nacional de Vigilância Sanitária). A calibração e aferição de instrumentos de medição são frequentemente exigidas para garantir que as empresas estejam em conformidade com essas normas. A não conformidade pode resultar em penalidades, multas e até mesmo na suspensão das operações.
Além disso, a calibração e aferição contribuem para a eficiência operacional. Quando os instrumentos de medição estão calibrados corretamente, as empresas podem otimizar seus processos, reduzindo desperdícios e melhorando a produtividade. Por exemplo, em uma linha de produção, a medição precisa de temperatura e pressão pode ajudar a manter as condições ideais de operação, evitando paradas não programadas e aumentando a eficiência do sistema. Isso se traduz em economia de custos e maior competitividade no mercado.
Os instrumentos de medição, como o Medidor de vazão ultrassônico, são exemplos de equipamentos que requerem calibração regular para garantir medições precisas. Esses dispositivos são amplamente utilizados em diversas aplicações, desde o monitoramento de sistemas de água até processos industriais complexos. A calibração adequada desses instrumentos assegura que as medições de vazão sejam confiáveis, permitindo que as empresas tomem decisões informadas com base em dados precisos.
Além disso, a calibração e aferição ajudam a prolongar a vida útil dos equipamentos. Instrumentos que não são calibrados regularmente podem sofrer desgastes mais rapidamente, resultando em custos adicionais com manutenção e substituição. Ao realizar a calibração de forma sistemática, as empresas podem identificar problemas potenciais antes que se tornem críticos, economizando tempo e recursos a longo prazo.
Por fim, a calibração e aferição promovem uma cultura de qualidade dentro das organizações. Quando as empresas investem em processos de calibração e aferição, elas demonstram um compromisso com a excelência e a melhoria contínua. Isso não apenas melhora a qualidade dos produtos, mas também aumenta a satisfação do cliente e a confiança na marca. Em um mercado cada vez mais competitivo, a reputação de uma empresa pode ser um diferencial significativo, e a calibração e aferição desempenham um papel fundamental nesse aspecto.
Em resumo, a calibração e aferição de instrumentos de medição são essenciais para garantir a qualidade, segurança e eficiência nas operações industriais. Esses processos não apenas ajudam a atender às normas regulatórias, mas também contribuem para a otimização dos processos produtivos e a satisfação do cliente. Investir em calibração e aferição é, portanto, um passo crucial para qualquer empresa que busca se destacar em um mercado competitivo e em constante evolução.
Métodos Comuns de Calibração e Aferição
A calibração e aferição de instrumentos de medição são processos essenciais para garantir a precisão e a confiabilidade dos dados obtidos em diversas aplicações industriais e laboratoriais. Existem vários métodos utilizados para realizar esses procedimentos, cada um com suas características e adequações específicas. Neste artigo, abordaremos os métodos mais comuns de calibração e aferição, destacando suas vantagens e aplicações.
Um dos métodos mais tradicionais de calibração é o método de comparação. Neste processo, o instrumento a ser calibrado é comparado a um padrão de referência conhecido, que possui uma precisão superior. O padrão pode ser um instrumento de medição calibrado por um laboratório acreditado ou um dispositivo que atenda a normas específicas. Durante a comparação, as leituras do instrumento em teste são registradas e comparadas com as do padrão. Se houver discrepâncias, ajustes são feitos no instrumento para garantir que suas medições estejam dentro das especificações desejadas.
Outro método comum é a calibração por ponto fixo. Neste caso, o instrumento é calibrado em pontos específicos de sua faixa de medição. Por exemplo, se um termômetro for calibrado, ele pode ser testado em temperaturas de 0°C, 25°C e 100°C. Esse método é útil para instrumentos que apresentam não linearidades em suas medições, pois permite identificar e corrigir desvios em diferentes pontos da faixa de operação. A calibração por ponto fixo é amplamente utilizada em indústrias que requerem medições precisas, como a farmacêutica e a alimentícia.
A calibração em múltiplos pontos é uma variação do método de ponto fixo, onde o instrumento é testado em vários pontos ao longo de sua faixa de medição. Esse método é especialmente eficaz para instrumentos que apresentam comportamento não linear, pois permite uma análise mais abrangente do desempenho do dispositivo. A calibração em múltiplos pontos é frequentemente utilizada em laboratórios de metrologia e em indústrias que exigem alta precisão nas medições.
Além dos métodos mencionados, a calibração por simulação é outra técnica utilizada, especialmente em instrumentos eletrônicos. Neste método, um sinal elétrico conhecido é gerado e aplicado ao instrumento em teste. O instrumento deve responder a esse sinal de acordo com suas especificações. A calibração por simulação é particularmente útil para dispositivos que não podem ser testados diretamente, como sensores de pressão e temperatura. Essa abordagem permite verificar o desempenho do instrumento em condições controladas, garantindo que ele funcione corretamente em situações reais.
A aferição, por sua vez, pode ser realizada através de métodos de verificação. Nesse caso, o instrumento é testado em relação a padrões de referência, mas sem a necessidade de ajustes. A aferição é geralmente utilizada para confirmar que um instrumento está operando dentro das especificações, sem a intenção de realizar ajustes. Esse método é comum em ambientes onde a precisão é crítica, mas onde ajustes frequentes não são viáveis, como em processos de produção contínua.
Outro método de aferição é a aferição em campo, que é realizada diretamente no local de uso do instrumento. Esse método é especialmente útil para instrumentos que não podem ser facilmente transportados para um laboratório de calibração. A aferição em campo permite que os operadores verifiquem a precisão dos instrumentos em suas condições reais de operação, garantindo que as medições sejam confiáveis. Muitas empresas de calibração de equipamentos oferecem serviços de aferição em campo, proporcionando conveniência e eficiência para os usuários.
Além dos métodos tradicionais, a tecnologia também trouxe inovações para a calibração e aferição. O uso de software de calibração e sistemas automatizados tem se tornado cada vez mais comum. Esses sistemas permitem que os processos de calibração sejam realizados de forma mais rápida e precisa, reduzindo a possibilidade de erro humano. A automação também facilita o registro e a análise de dados, permitindo que as empresas monitorem o desempenho de seus instrumentos ao longo do tempo.
Por fim, é importante ressaltar que a escolha do método de calibração e aferição deve levar em consideração diversos fatores, como o tipo de instrumento, a faixa de medição, a precisão requerida e as condições de operação. Cada método possui suas vantagens e limitações, e a seleção adequada é fundamental para garantir resultados confiáveis. Além disso, a calibração e aferição devem ser realizadas por profissionais qualificados, que possuam conhecimento técnico e experiência na área, assegurando que os procedimentos sejam realizados de acordo com as normas e padrões estabelecidos.
Em resumo, os métodos comuns de calibração e aferição incluem comparação, ponto fixo, múltiplos pontos, simulação e verificação. Cada um desses métodos possui suas aplicações específicas e é fundamental para garantir a precisão e a confiabilidade dos instrumentos de medição. A adoção de práticas adequadas de calibração e aferição é essencial para a qualidade dos processos industriais e laboratoriais, contribuindo para a segurança e a eficiência das operações.
Frequência Recomendada para Calibração de Instrumentos
A calibração de instrumentos de medição é um processo essencial para garantir a precisão e a confiabilidade dos dados obtidos em diversas aplicações industriais e laboratoriais. No entanto, a eficácia desse processo depende não apenas da qualidade da calibração em si, mas também da frequência com que ela é realizada. Neste artigo, discutiremos a frequência recomendada para a calibração de instrumentos, considerando fatores que influenciam essa periodicidade e a importância de manter um cronograma adequado.
A frequência de calibração pode variar significativamente dependendo do tipo de instrumento, da aplicação em que ele é utilizado e das condições ambientais a que está exposto. Por exemplo, instrumentos que operam em ambientes agressivos, como fábricas químicas ou petroquímicas, podem exigir calibrações mais frequentes devido ao desgaste acelerado e à possibilidade de contaminação. Em contrapartida, instrumentos utilizados em ambientes controlados, como laboratórios, podem ter uma frequência de calibração mais espaçada.
Um dos principais fatores a serem considerados ao determinar a frequência de calibração é a criticidade da medição. Em setores onde a precisão é vital, como na indústria farmacêutica e alimentícia, a calibração deve ser realizada com maior frequência. Por exemplo, um medidor de vazão utilizado em um processo de produção de medicamentos deve ser calibrado regularmente para garantir que as dosagens estejam corretas e que os produtos atendam aos padrões de qualidade. A não conformidade pode resultar em produtos inseguros e em sérios problemas legais e de reputação para a empresa.
Além da criticidade da medição, a frequência de calibração também deve levar em conta a estabilidade do instrumento. Alguns instrumentos são projetados para manter sua precisão por longos períodos, enquanto outros podem apresentar desvios mais rapidamente. A estabilidade pode ser influenciada por fatores como temperatura, umidade e vibração. Portanto, é importante que as empresas realizem uma avaliação inicial da estabilidade de seus instrumentos e ajustem a frequência de calibração de acordo.
Outro aspecto a ser considerado é a frequência de uso do instrumento. Instrumentos que são utilizados com alta frequência, como aqueles em linhas de produção, podem exigir calibrações mais regulares. O uso constante pode levar ao desgaste e à deterioração, resultando em medições imprecisas. Por outro lado, instrumentos que são utilizados esporadicamente podem ter uma frequência de calibração mais espaçada, desde que sejam mantidos em boas condições e armazenados adequadamente quando não estiverem em uso.
As recomendações de calibração também podem ser influenciadas por normas e regulamentos específicos do setor. Muitas indústrias são obrigadas a seguir diretrizes estabelecidas por órgãos reguladores, como a ISO (Organização Internacional de Normalização) e a ANVISA (Agência Nacional de Vigilância Sanitária). Essas normas frequentemente incluem requisitos sobre a frequência de calibração, e as empresas devem garantir que estão em conformidade para evitar penalidades e garantir a qualidade de seus produtos.
Além disso, é importante que as empresas implementem um sistema de gerenciamento de calibração. Esse sistema deve incluir um cronograma de calibração, registros de calibração anteriores e um plano de ação para lidar com instrumentos que apresentem desvios. A documentação adequada é fundamental para garantir a rastreabilidade e a conformidade com as normas regulatórias. Um sistema bem estruturado ajuda a evitar esquecimentos e garante que todos os instrumentos sejam calibrados dentro dos prazos estabelecidos.
Em muitos casos, as empresas optam por contratar serviços de calibração de terceiros, especialmente quando não possuem os recursos ou a expertise interna para realizar a calibração de forma eficaz. Ao escolher uma empresa de calibração, é importante verificar se ela é acreditada e se segue as normas e padrões reconhecidos. A calibração realizada por profissionais qualificados garante que os instrumentos sejam calibrados de acordo com as melhores práticas e que os resultados sejam confiáveis.
Por fim, a frequência recomendada para a calibração de instrumentos deve ser revisada periodicamente. À medida que as condições de operação mudam, ou à medida que novos instrumentos são introduzidos, pode ser necessário ajustar a frequência de calibração. As empresas devem estar atentas a qualquer sinal de que um instrumento pode não estar funcionando corretamente, como leituras inconsistentes ou comportamentos anômalos, e devem agir rapidamente para realizar a calibração necessária.
Em resumo, a frequência recomendada para a calibração de instrumentos de medição depende de diversos fatores, incluindo a criticidade da medição, a estabilidade do instrumento, a frequência de uso e as normas regulatórias. Manter um cronograma adequado de calibração é fundamental para garantir a precisão e a confiabilidade das medições, contribuindo para a qualidade dos produtos e a segurança das operações. A implementação de um sistema de gerenciamento de calibração e a escolha de empresas acreditadas para realizar o serviço são práticas recomendadas que ajudam a garantir a eficácia do processo de calibração.
Erros Comuns na Calibração e Como Evitá-los
A calibração de instrumentos de medição é um processo crítico que garante a precisão e a confiabilidade das medições em diversas aplicações industriais e laboratoriais. No entanto, existem erros comuns que podem ocorrer durante esse processo, comprometendo a eficácia da calibração e resultando em medições imprecisas. Neste artigo, discutiremos os erros mais frequentes na calibração e como evitá-los, assegurando que os instrumentos funcionem corretamente e atendam aos padrões exigidos.
Um dos erros mais comuns na calibração é a falta de um padrão de referência adequado. A calibração deve ser realizada em comparação com um padrão que tenha uma precisão superior ao instrumento em teste. Se o padrão utilizado não for confiável ou não estiver devidamente calibrado, as medições do instrumento em teste também estarão comprometidas. Para evitar esse erro, é fundamental utilizar padrões de referência que sejam rastreáveis a laboratórios acreditados e que atendam às normas relevantes. Além disso, é importante verificar a validade da calibração do padrão antes de utilizá-lo.
Outro erro frequente é a calibração em condições inadequadas. A temperatura, umidade e pressão atmosférica podem influenciar as medições e, portanto, devem ser controladas durante o processo de calibração. Realizar a calibração em ambientes que não atendem às especificações recomendadas pode resultar em desvios nas medições. Para evitar esse problema, as empresas devem garantir que a calibração seja realizada em condições ambientais controladas e que os instrumentos estejam estabilizados antes do início do processo.
A falta de treinamento adequado dos profissionais responsáveis pela calibração também é um erro comum. A calibração é um processo técnico que requer conhecimento e habilidades específicas. Profissionais não treinados podem cometer erros ao realizar medições, ajustes ou interpretações dos resultados. Para evitar esse erro, é essencial que as empresas invistam em treinamento contínuo para suas equipes, garantindo que todos os envolvidos no processo de calibração compreendam as melhores práticas e os procedimentos corretos.
Além disso, a falta de documentação adequada pode levar a erros na calibração. Registros precisos são fundamentais para garantir a rastreabilidade e a conformidade com as normas regulatórias. A ausência de documentação pode resultar em dificuldades na verificação da calibração e na identificação de problemas. Para evitar esse erro, as empresas devem implementar um sistema de gerenciamento de calibração que inclua a documentação de todos os procedimentos, resultados e ações corretivas realizadas. Isso não apenas ajuda a manter a conformidade, mas também facilita a identificação de tendências e problemas recorrentes.
Outro erro comum é a calibração em intervalos inadequados. A frequência de calibração deve ser determinada com base em fatores como a criticidade da medição, a estabilidade do instrumento e as condições de operação. Calibrar instrumentos com muita frequência pode resultar em custos desnecessários, enquanto a calibração em intervalos muito longos pode comprometer a precisão das medições. Para evitar esse erro, as empresas devem estabelecer um cronograma de calibração que leve em consideração todos esses fatores e que seja revisado periodicamente.
A falta de verificação pós-calibração é outro erro que pode comprometer a eficácia do processo. Após a calibração, é fundamental realizar testes para garantir que o instrumento esteja funcionando corretamente e que as medições estejam dentro das especificações. Ignorar essa etapa pode resultar em instrumentos que não estão operando conforme esperado. Para evitar esse erro, as empresas devem incluir a verificação pós-calibração como parte do processo padrão, garantindo que todos os instrumentos sejam testados antes de serem colocados de volta em operação.
Além disso, a escolha inadequada da empresa de calibração pode levar a erros. É importante selecionar uma empresa de calibração de instrumentos de medição que seja acreditada e que siga as normas e padrões reconhecidos. A calibração realizada por profissionais qualificados garante que os instrumentos sejam calibrados de acordo com as melhores práticas e que os resultados sejam confiáveis. As empresas devem realizar uma pesquisa cuidadosa ao escolher um prestador de serviços de calibração, verificando suas credenciais e referências.
Por fim, a falta de manutenção regular dos instrumentos também pode afetar a calibração. Instrumentos que não são mantidos adequadamente podem apresentar desgastes e falhas que comprometem suas medições. Para evitar esse erro, as empresas devem implementar um programa de manutenção preventiva que inclua inspeções regulares e reparos conforme necessário. A manutenção adequada ajuda a garantir que os instrumentos permaneçam em boas condições e que as medições sejam precisas ao longo do tempo.
Em resumo, os erros comuns na calibração incluem a falta de padrões de referência adequados, condições inadequadas, falta de treinamento, documentação insuficiente, calibração em intervalos inadequados, falta de verificação pós-calibração, escolha inadequada da empresa de calibração e falta de manutenção regular. Ao estar ciente desses erros e implementar medidas para evitá-los, as empresas podem garantir que seus instrumentos de medição funcionem corretamente e atendam aos padrões exigidos, contribuindo para a qualidade e a segurança de seus processos.
Em conclusão, a calibração e aferição de instrumentos de medição são essenciais para a manutenção da qualidade e segurança em processos industriais e laboratoriais. A compreensão da importância desses procedimentos, juntamente com o conhecimento dos métodos adequados, da frequência recomendada e dos erros comuns a serem evitados, permite que as empresas garantam medições precisas e confiáveis. Investir em calibração e aferição não apenas melhora a eficiência operacional, mas também protege a reputação da empresa e assegura a conformidade com normas regulatórias. Portanto, é fundamental que as organizações adotem práticas rigorosas de calibração e aferição, promovendo uma cultura de qualidade e excelência em suas operações.