Calibração de Transmissor de Pressão: Como Garantir Precisão e Confiabilidade em Seus Processos
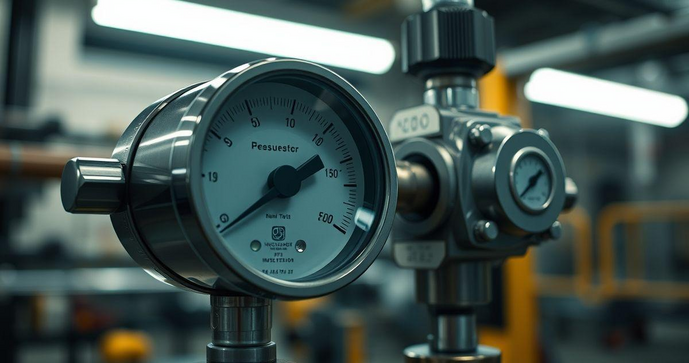
Por: Rafael - 27 de Março de 2025
A calibração de transmissor de pressão é um processo fundamental para garantir a precisão e a confiabilidade em sistemas de medição industrial. Com a crescente demanda por eficiência e segurança nas operações, a calibração adequada desses dispositivos se torna essencial. Neste artigo, abordaremos a importância da calibração, os passos necessários para realizá-la corretamente e os cuidados que devem ser tomados para evitar erros comuns. Além disso, discutiremos a manutenção regular dos transmissores, assegurando que eles operem sempre em condições ideais.
Importância da Calibração de Transmissores de Pressão na Indústria
A calibração de transmissores de pressão é um aspecto crítico na operação de diversos setores industriais, incluindo petroquímica, farmacêutica, alimentícia e de energia. Esses dispositivos são responsáveis por medir a pressão de fluidos em sistemas, e sua precisão é vital para garantir a segurança, eficiência e qualidade dos processos. A seguir, discutiremos a importância da calibração de transmissores de pressão e como ela impacta diretamente a operação industrial.
Um dos principais motivos para a calibração regular dos transmissores de pressão é a segurança. Em indústrias onde a pressão de fluidos pode afetar a integridade de equipamentos e a segurança dos trabalhadores, a precisão das medições é fundamental. Um transmissor descalibrado pode levar a leituras incorretas, resultando em pressões excessivas ou insuficientes. Isso pode causar falhas catastróficas, como explosões ou vazamentos, colocando em risco a vida dos funcionários e a operação da planta.
Além da segurança, a calibração de transmissores de pressão também é essencial para a eficiência operacional. Processos industriais frequentemente dependem de medições precisas para otimizar o uso de recursos, como energia e matérias-primas. Um transmissor que não está calibrado corretamente pode levar a desperdícios significativos, aumentando os custos operacionais. Por exemplo, em sistemas de controle de processos, uma leitura imprecisa pode resultar em ajustes inadequados, afetando a qualidade do produto final e a produtividade da linha de produção.
A calibração também desempenha um papel crucial na conformidade regulatória. Muitas indústrias são obrigadas a seguir normas e regulamentos rigorosos que exigem a calibração regular de equipamentos de medição. A não conformidade pode resultar em penalidades financeiras, interrupções na produção e danos à reputação da empresa. Portanto, manter um programa de calibração eficaz não apenas assegura a precisão das medições, mas também ajuda as empresas a permanecerem em conformidade com as exigências legais.
Outro aspecto importante da calibração de transmissores de pressão é a manutenção da qualidade do produto. Em setores como o alimentício e farmacêutico, onde a qualidade é crítica, a precisão das medições de pressão pode afetar diretamente a integridade do produto. Por exemplo, em processos de pasteurização, a pressão deve ser mantida dentro de limites específicos para garantir a eficácia do tratamento térmico. Se um transmissor de pressão estiver descalibrado, isso pode resultar em produtos que não atendem aos padrões de qualidade, levando a recalls e perda de confiança do consumidor.
Além disso, a calibração regular dos transmissores de pressão contribui para a longevidade do equipamento. Dispositivos que não são calibrados podem sofrer desgaste prematuro devido a leituras incorretas que levam a operações fora das especificações. Isso pode resultar em falhas mecânicas e a necessidade de substituições frequentes, aumentando os custos de manutenção e operação. Por outro lado, um programa de calibração bem estruturado pode ajudar a identificar problemas antes que se tornem críticos, permitindo que as empresas realizem manutenções preventivas e prolonguem a vida útil dos equipamentos.
Para garantir a eficácia da calibração, é importante que as empresas utilizem equipamentos de calibração de alta qualidade e sigam procedimentos padronizados. A calibração deve ser realizada por profissionais qualificados que compreendam as especificações do transmissor e as condições de operação. Além disso, a documentação adequada das calibrações realizadas é essencial para rastrear o histórico de manutenção e garantir a conformidade com as normas regulatórias.
Um exemplo de equipamento que pode ser utilizado em conjunto com transmissores de pressão é o Medidor de vazão ultrassônico, que oferece medições precisas de fluxo em sistemas de tubulação. A integração de diferentes dispositivos de medição, como transmissores de pressão e medidores de vazão, pode proporcionar uma visão mais abrangente do desempenho do sistema, permitindo ajustes mais precisos e eficientes.
Em resumo, a calibração de transmissores de pressão é uma prática indispensável na indústria moderna. Ela garante a segurança, eficiência, conformidade regulatória e qualidade do produto, além de contribuir para a longevidade do equipamento. As empresas que investem em programas de calibração eficazes não apenas protegem seus funcionários e ativos, mas também melhoram sua competitividade no mercado. Portanto, é fundamental que as indústrias reconheçam a importância da calibração e implementem práticas adequadas para garantir medições precisas e confiáveis.
Passo a Passo para Realizar a Calibração de Transmissores
A calibração de transmissores de pressão é um processo essencial para garantir a precisão e a confiabilidade das medições em sistemas industriais. Realizar a calibração de forma adequada não apenas assegura a segurança e a eficiência operacional, mas também ajuda a manter a conformidade com as normas regulatórias. A seguir, apresentamos um passo a passo detalhado para realizar a calibração de transmissores de pressão.
1. Preparação e Planejamento
Antes de iniciar o processo de calibração, é fundamental realizar um planejamento adequado. Isso inclui a definição do cronograma de calibração, a seleção dos equipamentos necessários e a designação de pessoal qualificado para realizar a calibração. É importante verificar se o transmissor de pressão está em boas condições e se não apresenta danos visíveis. Além disso, deve-se garantir que o ambiente de calibração esteja limpo e livre de interferências que possam afetar as medições.
2. Reunir Equipamentos Necessários
Para realizar a calibração, você precisará de alguns equipamentos essenciais, como um calibrador de pressão, que pode ser um manômetro de referência ou um calibrador eletrônico. O calibrador deve ter uma precisão superior à do transmissor que está sendo calibrado. Além disso, é importante ter ferramentas básicas, como chaves de fenda, alicates e cabos de conexão, para facilitar o processo. Se necessário, consulte Empresas de calibração de equipamentos para obter suporte e equipamentos adequados.
3. Desconectar o Transmissor
Antes de iniciar a calibração, é necessário desconectar o transmissor de pressão do sistema. Isso garante que não haja interferências durante o processo de calibração. Certifique-se de seguir os procedimentos de segurança ao desconectar o transmissor, evitando vazamentos de fluidos ou danos ao equipamento. Após a desconexão, verifique se o transmissor está completamente isolado do sistema.
4. Conectar o Calibrador de Pressão
Com o transmissor desconectado, conecte o calibrador de pressão à entrada do transmissor. É importante garantir que as conexões estejam firmes e seguras para evitar vazamentos. Após a conexão, ligue o calibrador e ajuste-o para a pressão de referência que será utilizada durante a calibração. Essa pressão deve ser escolhida com base nas especificações do transmissor e nas condições de operação.
5. Realizar a Calibração
Inicie o processo de calibração aplicando a pressão de referência ao transmissor. Observe a leitura do transmissor e compare-a com a leitura do calibrador. Se as leituras não coincidirem, será necessário ajustar o transmissor. A maioria dos transmissores possui um botão de ajuste ou um software de configuração que permite calibrar a saída do dispositivo. Siga as instruções do fabricante para realizar os ajustes necessários.
Repita esse processo em diferentes pontos de pressão, cobrindo toda a faixa de operação do transmissor. É recomendável realizar a calibração em pelo menos três pontos: o ponto baixo, o ponto médio e o ponto alto da faixa de medição. Isso garante que o transmissor esteja calibrado de forma precisa em toda a sua faixa de operação.
6. Documentar os Resultados
Após concluir a calibração, é fundamental documentar todos os resultados obtidos. Registre as leituras do transmissor e do calibrador em cada ponto de pressão, bem como os ajustes realizados. Essa documentação é importante para rastrear o histórico de calibração do transmissor e para garantir a conformidade com as normas regulatórias. Além disso, a documentação pode ser útil para futuras manutenções e calibrações.
7. Desconectar e Reinstalar o Transmissor
Depois de concluir a calibração e documentar os resultados, desconecte o calibrador de pressão do transmissor. Em seguida, reinstale o transmissor no sistema, garantindo que todas as conexões estejam firmes e seguras. Verifique se não há vazamentos antes de reiniciar o sistema. É importante realizar um teste final para garantir que o transmissor esteja funcionando corretamente após a calibração.
8. Manutenção e Verificação Regular
A calibração não deve ser vista como uma tarefa única, mas sim como parte de um programa contínuo de manutenção. É importante estabelecer um cronograma de calibração regular com base nas recomendações do fabricante e nas condições de operação. A verificação periódica dos transmissores de pressão ajuda a garantir que eles permaneçam precisos e confiáveis ao longo do tempo.
Em resumo, a calibração de transmissores de pressão é um processo crítico que requer atenção aos detalhes e um planejamento cuidadoso. Seguir este passo a passo garantirá que os transmissores operem com precisão, contribuindo para a segurança e eficiência dos processos industriais. Ao investir tempo e recursos na calibração adequada, as empresas podem evitar problemas futuros e garantir a qualidade de suas operações.
Erros Comuns na Calibração de Transmissores de Pressão
A calibração de transmissores de pressão é um processo crítico para garantir a precisão e a confiabilidade das medições em sistemas industriais. No entanto, existem diversos erros que podem ocorrer durante esse processo, comprometendo a eficácia da calibração e, consequentemente, a segurança e a eficiência das operações. A seguir, discutiremos os erros mais comuns na calibração de transmissores de pressão e como evitá-los.
1. Falta de Planejamento Adequado
Um dos erros mais frequentes na calibração de transmissores de pressão é a falta de um planejamento adequado. Muitas vezes, as empresas não estabelecem um cronograma de calibração ou não designam pessoal qualificado para realizar a tarefa. Isso pode levar a calibrações irregulares e à falta de documentação necessária. Para evitar esse erro, é fundamental criar um plano de calibração que inclua a frequência das calibrações, os responsáveis e os procedimentos a serem seguidos.
2. Uso de Equipamentos de Calibração Inadequados
Outro erro comum é o uso de equipamentos de calibração que não atendem às especificações necessárias. Um calibrador de pressão deve ter uma precisão superior à do transmissor que está sendo calibrado. Se um equipamento inadequado for utilizado, as medições podem ser imprecisas, resultando em uma calibração incorreta. Portanto, é essencial verificar a calibração e a precisão dos equipamentos utilizados antes de iniciar o processo.
3. Ignorar as Condições Ambientais
As condições ambientais podem ter um impacto significativo nas medições de pressão. Fatores como temperatura, umidade e vibração podem afetar o desempenho do transmissor e do equipamento de calibração. Ignorar essas condições pode levar a resultados imprecisos. Para evitar esse erro, é importante realizar a calibração em um ambiente controlado, onde as condições possam ser monitoradas e mantidas dentro dos limites especificados pelo fabricante.
4. Não Realizar a Calibração em Vários Pontos
Calibrar um transmissor de pressão apenas em um único ponto pode resultar em medições imprecisas em toda a faixa de operação. É recomendável realizar a calibração em pelo menos três pontos: o ponto baixo, o ponto médio e o ponto alto da faixa de medição. Isso garante que o transmissor esteja calibrado de forma precisa em toda a sua faixa de operação. Ignorar essa prática pode comprometer a precisão das medições em condições reais de operação.
5. Falta de Documentação
A documentação é uma parte crucial do processo de calibração. Muitos profissionais negligenciam a importância de registrar os resultados da calibração, os ajustes realizados e as condições em que a calibração foi realizada. A falta de documentação pode dificultar a rastreabilidade e a conformidade com as normas regulatórias. Para evitar esse erro, é fundamental manter registros detalhados de todas as calibrações realizadas, incluindo datas, resultados e assinaturas dos responsáveis.
6. Não Treinar Adequadamente a Equipe
A calibração de transmissores de pressão deve ser realizada por profissionais qualificados e treinados. Um erro comum é não fornecer o treinamento adequado à equipe responsável pela calibração. Isso pode resultar em procedimentos inadequados e na realização de ajustes incorretos. Para evitar esse problema, as empresas devem investir em treinamentos regulares e garantir que a equipe esteja atualizada sobre as melhores práticas e procedimentos de calibração.
7. Ignorar a Manutenção do Equipamento
A manutenção regular dos transmissores de pressão e dos equipamentos de calibração é essencial para garantir medições precisas. Ignorar a manutenção pode levar a falhas nos dispositivos e a medições imprecisas. É importante estabelecer um programa de manutenção preventiva que inclua inspeções regulares e a substituição de peças desgastadas. Isso ajudará a garantir que os transmissores e os equipamentos de calibração estejam sempre em boas condições de funcionamento.
8. Não Considerar a Interferência de Outros Equipamentos
Em ambientes industriais, a interferência de outros equipamentos pode afetar as medições de pressão. Por exemplo, vibrações de máquinas próximas ou campos eletromagnéticos podem impactar o desempenho do transmissor. Ignorar essa interferência pode resultar em medições imprecisas. Para evitar esse erro, é importante avaliar o ambiente de calibração e, se necessário, realizar a calibração em um local onde a interferência possa ser minimizada.
9. Não Realizar Testes Finais
Após a calibração, é fundamental realizar testes finais para garantir que o transmissor esteja funcionando corretamente. Muitos profissionais cometem o erro de não realizar esses testes, o que pode levar a problemas não detectados. Realizar testes finais ajuda a confirmar que o transmissor está operando dentro das especificações e que a calibração foi bem-sucedida. Isso é especialmente importante em aplicações críticas, onde a precisão é vital.
10. Subestimar a Importância da Calibração Contínua
A calibração não deve ser vista como uma tarefa única, mas sim como parte de um programa contínuo de manutenção. Muitas empresas subestimam a importância da calibração regular e acabam enfrentando problemas devido a medições imprecisas. Estabelecer um cronograma de calibração contínua é essencial para garantir que os transmissores de pressão permaneçam precisos e confiáveis ao longo do tempo.
Em resumo, a calibração de transmissores de pressão é um processo crítico que requer atenção aos detalhes e um planejamento cuidadoso. Evitar os erros comuns mencionados acima ajudará a garantir que os transmissores operem com precisão, contribuindo para a segurança e eficiência dos processos industriais. Ao investir tempo e recursos na calibração adequada, as empresas podem evitar problemas futuros e garantir a qualidade de suas operações. Além disso, a utilização de dispositivos como o Medidor de vazão pode complementar a precisão das medições, proporcionando uma visão mais abrangente do desempenho do sistema.
Manutenção e Verificação Regular de Transmissores de Pressão
A manutenção e verificação regular de transmissores de pressão são fundamentais para garantir a precisão e a confiabilidade das medições em sistemas industriais. Esses dispositivos desempenham um papel crucial em diversas aplicações, desde o controle de processos até a segurança operacional. Portanto, é essencial implementar um programa de manutenção eficaz que assegure o funcionamento adequado dos transmissores ao longo do tempo. A seguir, discutiremos a importância da manutenção, as melhores práticas e os benefícios de realizar verificações regulares.
1. Importância da Manutenção Regular
A manutenção regular dos transmissores de pressão é vital para evitar falhas e garantir medições precisas. Com o tempo, os componentes dos transmissores podem sofrer desgaste devido a fatores como vibrações, variações de temperatura e exposição a substâncias químicas. Esses fatores podem afetar a precisão das medições e, consequentemente, a segurança e a eficiência dos processos industriais. A manutenção preventiva ajuda a identificar problemas antes que se tornem críticos, evitando paradas não programadas e custos elevados de reparo.
2. Tipos de Manutenção
Existem diferentes tipos de manutenção que podem ser aplicados aos transmissores de pressão, incluindo:
- Manutenção Preventiva: Envolve inspeções regulares e serviços programados para garantir que os transmissores estejam funcionando corretamente. Isso pode incluir a limpeza, lubrificação e ajustes necessários.
- Manutenção Corretiva: Realizada quando um problema é identificado. Essa manutenção visa corrigir falhas e restaurar o funcionamento adequado do transmissor.
- Manutenção Preditiva: Utiliza técnicas de monitoramento e análise de dados para prever falhas antes que ocorram. Isso pode incluir a análise de vibrações, termografia e monitoramento de desempenho.
3. Verificação de Desempenho
Além da manutenção, a verificação regular do desempenho dos transmissores de pressão é essencial. Isso envolve a realização de testes para garantir que os dispositivos estejam operando dentro das especificações. A verificação deve incluir:
- Testes de Calibração: Realizar calibrações periódicas para garantir que as medições estejam corretas. Isso deve ser feito em intervalos regulares, conforme recomendado pelo fabricante ou pelas normas da indústria.
- Testes de Resposta: Avaliar a resposta do transmissor a mudanças de pressão. Isso ajuda a identificar atrasos ou imprecisões na medição.
- Testes de Estabilidade: Monitorar a estabilidade das medições ao longo do tempo. Isso é importante para garantir que o transmissor não apresente deriva nas leituras.
4. Documentação e Registro
Manter registros detalhados de todas as atividades de manutenção e verificação é crucial. Isso inclui a documentação de calibrações, inspeções, ajustes e quaisquer problemas identificados. A documentação não apenas ajuda a rastrear o histórico de manutenção, mas também é essencial para garantir a conformidade com as normas regulatórias. Além disso, esses registros podem ser úteis para futuras manutenções e para a análise de tendências de desempenho.
5. Treinamento da Equipe
Um aspecto muitas vezes negligenciado na manutenção de transmissores de pressão é o treinamento da equipe responsável. É fundamental que os profissionais que realizam a manutenção e verificação estejam devidamente treinados e atualizados sobre as melhores práticas e procedimentos. Isso inclui o conhecimento sobre os tipos de transmissores, suas especificações e os métodos de calibração. Investir em treinamento regular pode aumentar a eficiência da equipe e reduzir a probabilidade de erros durante a manutenção.
6. Consultoria Especializada
Em alguns casos, pode ser benéfico contar com a ajuda de uma Empresa de calibração de instrumentos de medição especializada. Essas empresas possuem conhecimento técnico e equipamentos adequados para realizar calibrações e manutenções de forma eficaz. Além disso, elas podem oferecer serviços de manutenção preditiva e corretiva, garantindo que os transmissores operem com a máxima eficiência.
7. Benefícios da Manutenção Regular
Implementar um programa de manutenção e verificação regular traz diversos benefícios, incluindo:
- Maior Precisão: A manutenção regular garante que os transmissores operem dentro das especificações, resultando em medições mais precisas.
- Redução de Custos: A identificação precoce de problemas pode evitar falhas catastróficas e reduzir os custos de reparo e substituição.
- Aumento da Vida Útil: A manutenção adequada pode prolongar a vida útil dos transmissores, resultando em menos substituições e investimentos a longo prazo.
- Conformidade Regulatória: Manter registros detalhados e realizar manutenções regulares ajuda a garantir a conformidade com as normas da indústria.
8. Conclusão
A manutenção e verificação regular de transmissores de pressão são essenciais para garantir a precisão e a confiabilidade das medições em sistemas industriais. Implementar um programa de manutenção eficaz, realizar verificações de desempenho e manter registros detalhados são práticas fundamentais para evitar falhas e garantir a segurança operacional. Ao investir na manutenção adequada, as empresas podem melhorar a eficiência de seus processos e prolongar a vida útil de seus equipamentos, assegurando um funcionamento contínuo e confiável.
Em resumo, a calibração de transmissores de pressão é uma prática indispensável para garantir a precisão e a segurança em sistemas de medição industrial. Através de um processo bem estruturado, que inclui planejamento, uso de equipamentos adequados e verificação regular, é possível evitar erros que comprometam a eficiência operacional. Além disso, a manutenção contínua e a documentação adequada são essenciais para assegurar que os transmissores permaneçam confiáveis ao longo do tempo. Ao investir na calibração e na manutenção desses dispositivos, as empresas não apenas protegem seus ativos e colaboradores, mas também melhoram a qualidade de seus processos e produtos, contribuindo para um ambiente industrial mais seguro e eficiente.