Calibração de Instrumentos RBC: Garantindo Precisão e Confiabilidade em Medições
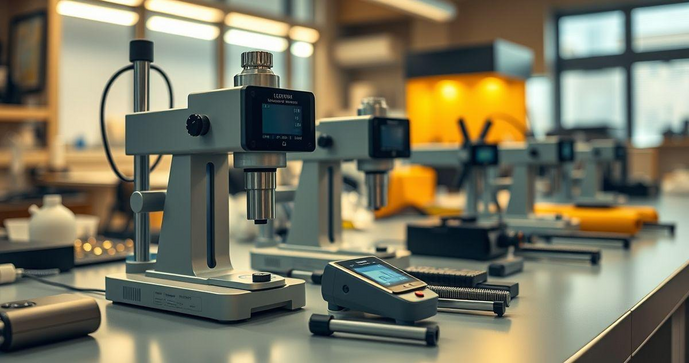
Por: Rafael - 23 de Fevereiro de 2025
A calibração de instrumentos RBC é um processo fundamental para garantir a precisão e a confiabilidade das medições em diversos setores, como laboratórios, indústrias e instituições de pesquisa. Este procedimento assegura que os instrumentos estejam funcionando corretamente, evitando erros que podem comprometer a qualidade dos resultados. Neste artigo, abordaremos a importância da calibração, os métodos utilizados, a frequência recomendada e os erros comuns que devem ser evitados durante o processo.
Importância da Calibração de Instrumentos RBC na Indústria
A calibração de instrumentos RBC (Reação de Balanço de Carga) é um aspecto crucial na indústria, pois garante que os equipamentos de medição estejam funcionando de maneira precisa e confiável. A precisão das medições é vital para a qualidade dos produtos, a segurança dos processos e a conformidade com as normas regulatórias. Neste contexto, a calibração se torna uma prática indispensável para qualquer organização que busca manter altos padrões de qualidade e eficiência.
Um dos principais motivos para a calibração de instrumentos RBC é a necessidade de garantir a precisão das medições. Instrumentos que não estão calibrados corretamente podem fornecer dados imprecisos, levando a decisões erradas que podem afetar a produção e a qualidade do produto final. Por exemplo, em indústrias químicas, a medição precisa de componentes é essencial para garantir que as reações ocorram conforme o esperado. Qualquer desvio nas medições pode resultar em produtos fora das especificações, o que pode causar desperdício e retrabalho.
Além disso, a calibração é fundamental para a segurança operacional. Em setores como o de alimentos e bebidas, a precisão nas medições é vital para garantir que os produtos sejam seguros para o consumo. Instrumentos que não estão calibrados podem levar a contaminações ou a produtos que não atendem aos padrões de segurança, colocando em risco a saúde dos consumidores e a reputação da empresa. Portanto, a calibração regular é uma prática que não deve ser negligenciada.
A calibração de instrumentos RBC também é importante para a conformidade com normas e regulamentos. Muitas indústrias são obrigadas a seguir normas específicas que exigem a calibração regular de seus instrumentos de medição. Por exemplo, a ISO 9001, uma norma internacional que estabelece critérios para sistemas de gestão da qualidade, exige que as organizações mantenham seus equipamentos calibrados e verificados. O não cumprimento dessas normas pode resultar em penalidades, perda de certificações e danos à reputação da empresa.
Outro aspecto relevante é a eficiência operacional. Instrumentos calibrados corretamente ajudam a otimizar os processos industriais, reduzindo o tempo de inatividade e aumentando a produtividade. Quando os instrumentos estão funcionando de maneira precisa, as medições são mais confiáveis, permitindo que os operadores tomem decisões informadas rapidamente. Isso é especialmente importante em ambientes de produção onde o tempo é um fator crítico.
Além disso, a calibração pode contribuir para a redução de custos. Embora possa parecer um investimento inicial, a calibração regular pode evitar custos mais altos associados a erros de medição, retrabalho e desperdício de materiais. Por exemplo, em uma linha de produção, um pequeno erro na medição de um componente pode resultar em grandes perdas financeiras se não for detectado a tempo. Portanto, a calibração é uma estratégia de gestão de riscos que pode levar a economias significativas a longo prazo.
Os instrumentos RBC são utilizados em diversas aplicações industriais, como medição de vazão, pressão, temperatura e nível. A precisão dessas medições é essencial para o controle de processos e a garantia da qualidade do produto. Por exemplo, o Medidor de vazão ultrassonônico é um dispositivo amplamente utilizado para medir a vazão de líquidos em tubulações. A calibração desse instrumento é fundamental para garantir que as medições de vazão sejam precisas, evitando problemas como a sub ou superdosagem de produtos químicos em processos industriais.
Além disso, a calibração de instrumentos RBC é uma prática que deve ser realizada por profissionais qualificados, que compreendam as especificações do equipamento e as normas aplicáveis. A calibração deve ser realizada em condições controladas, utilizando padrões de referência que garantam a precisão das medições. Isso assegura que os resultados obtidos sejam confiáveis e que os instrumentos estejam em conformidade com as exigências do setor.
Em resumo, a calibração de instrumentos RBC na indústria é de extrema importância para garantir a precisão das medições, a segurança operacional, a conformidade com normas e regulamentos, a eficiência operacional e a redução de custos. As empresas que investem na calibração regular de seus instrumentos não apenas melhoram a qualidade de seus produtos, mas também fortalecem sua posição no mercado, garantindo a satisfação do cliente e a sustentabilidade de suas operações. Portanto, a calibração deve ser vista como uma prática essencial e estratégica para qualquer organização que busca excelência em seus processos industriais.
Métodos Comuns de Calibração de Instrumentos RBC
A calibração de instrumentos RBC (Reação de Balanço de Carga) é um processo essencial para garantir a precisão e a confiabilidade das medições em diversas aplicações industriais. Existem vários métodos de calibração que podem ser utilizados, dependendo do tipo de instrumento, da aplicação e das condições específicas do ambiente de trabalho. Neste artigo, abordaremos os métodos mais comuns de calibração de instrumentos RBC, destacando suas características e aplicações.
Um dos métodos mais tradicionais de calibração é o método de comparação. Neste processo, o instrumento a ser calibrado é comparado a um padrão de referência conhecido, que possui uma precisão superior. O padrão pode ser um instrumento calibrado previamente ou um dispositivo de medição que atenda a normas específicas. Durante a calibração, o instrumento em teste é submetido a uma série de medições em diferentes pontos de operação, e os resultados são comparados com os valores do padrão. Essa abordagem é amplamente utilizada em laboratórios e indústrias, pois permite identificar desvios e ajustar o instrumento conforme necessário.
Outro método comum é a calibração por ponto fixo. Neste caso, o instrumento é calibrado em um ou mais pontos específicos de operação, que são escolhidos com base nas condições de uso mais frequentes. A calibração por ponto fixo é especialmente útil para instrumentos que operam em faixas limitadas de medição, como sensores de temperatura ou pressão. Esse método é mais simples e rápido, mas pode não fornecer uma visão completa do desempenho do instrumento em toda a sua faixa de operação. Portanto, é importante considerar as características do instrumento e as necessidades da aplicação ao escolher este método.
A calibração em campo é outro método que tem ganhado popularidade, especialmente em indústrias que utilizam instrumentos em ambientes externos ou em locais de difícil acesso. Neste caso, a calibração é realizada no local de instalação do instrumento, utilizando equipamentos portáteis e padrões de referência. A calibração em campo é vantajosa porque permite que os instrumentos sejam ajustados sem a necessidade de removê-los do local de operação, minimizando o tempo de inatividade e garantindo que as medições sejam precisas em condições reais de uso. No entanto, é fundamental que os profissionais responsáveis pela calibração em campo sejam devidamente treinados e qualificados para garantir a precisão dos resultados.
Além dos métodos mencionados, a calibração por simulação é uma técnica que tem se tornado cada vez mais comum, especialmente em aplicações que envolvem medições complexas. Neste método, um simulador é utilizado para gerar sinais de entrada que imitam as condições reais de operação do instrumento. Isso permite que o instrumento seja testado em uma variedade de cenários sem a necessidade de um ambiente físico específico. A calibração por simulação é particularmente útil para instrumentos eletrônicos e sistemas de controle, onde as condições de operação podem variar significativamente.
Outro aspecto importante a ser considerado na calibração de instrumentos RBC é a frequência com que a calibração deve ser realizada. A frequência ideal depende de vários fatores, incluindo a criticidade da aplicação, as condições de operação e as recomendações do fabricante. Em geral, instrumentos que são utilizados em ambientes mais rigorosos ou que são críticos para a segurança e a qualidade do produto devem ser calibrados com mais frequência. Muitas empresas optam por estabelecer um cronograma de calibração regular, que pode ser gerenciado internamente ou por meio de empresas de calibração de equipamentos especializadas.
Além dos métodos de calibração, é fundamental que as empresas adotem boas práticas de documentação e registro dos resultados de calibração. Manter um histórico detalhado das calibrações realizadas, incluindo datas, resultados e ajustes feitos, é essencial para garantir a rastreabilidade e a conformidade com normas e regulamentos. Essa documentação também pode ser útil para auditorias e inspeções, além de ajudar a identificar tendências de desempenho ao longo do tempo.
Por fim, a escolha do método de calibração adequado deve levar em consideração não apenas as características do instrumento, mas também as necessidades específicas da aplicação e as condições do ambiente de trabalho. A calibração é uma prática que requer conhecimento técnico e experiência, e é recomendável que as empresas busquem a orientação de profissionais qualificados para garantir que os instrumentos sejam calibrados corretamente e que os resultados sejam confiáveis.
Em resumo, os métodos comuns de calibração de instrumentos RBC incluem a calibração por comparação, calibração por ponto fixo, calibração em campo e calibração por simulação. Cada um desses métodos possui suas vantagens e desvantagens, e a escolha do método mais adequado deve ser baseada nas necessidades específicas da aplicação e nas características do instrumento. A calibração regular e adequada é fundamental para garantir a precisão das medições e a qualidade dos processos industriais, contribuindo para a segurança e a eficiência operacional.
Frequência Recomendada para Calibração de Instrumentos RBC
A calibração de instrumentos RBC (Reação de Balanço de Carga) é uma prática essencial para garantir a precisão e a confiabilidade das medições em diversas aplicações industriais. No entanto, a eficácia da calibração depende não apenas da qualidade do processo, mas também da frequência com que essa calibração é realizada. Neste artigo, discutiremos a frequência recomendada para a calibração de instrumentos RBC, considerando fatores que influenciam essa periodicidade e as melhores práticas a serem adotadas.
A frequência de calibração de instrumentos RBC pode variar significativamente dependendo de vários fatores, incluindo o tipo de instrumento, a criticidade da aplicação, as condições de operação e as recomendações do fabricante. Em geral, instrumentos utilizados em ambientes rigorosos ou que desempenham um papel crítico na segurança e na qualidade do produto devem ser calibrados com mais frequência. Por exemplo, um medidor de vazão utilizado em um processo químico pode exigir calibrações mensais, enquanto um instrumento menos crítico pode ser calibrado anualmente.
Um dos principais fatores que influenciam a frequência de calibração é a criticidade da aplicação. Em setores como alimentos e bebidas, farmacêutico e petroquímico, a precisão das medições é vital para garantir a segurança do produto e a conformidade com as normas regulatórias. Nesses casos, a calibração deve ser realizada com maior frequência para evitar riscos à saúde pública e garantir a qualidade do produto final. Por outro lado, em aplicações menos críticas, a calibração pode ser realizada em intervalos mais longos, desde que os instrumentos estejam em boas condições de operação.
As condições de operação também desempenham um papel importante na determinação da frequência de calibração. Instrumentos que operam em ambientes adversos, como altas temperaturas, umidade, vibrações ou exposição a produtos químicos, podem sofrer desgastes mais rapidamente e, portanto, necessitar de calibrações mais frequentes. Por exemplo, um instrumento utilizado em uma linha de produção de alimentos pode estar sujeito a contaminações e variações de temperatura, exigindo uma calibração mais rigorosa. Em contrapartida, instrumentos que operam em ambientes controlados e estáveis podem ter uma frequência de calibração mais espaçada.
Além disso, a frequência de calibração pode ser influenciada pelo histórico de desempenho do instrumento. Se um instrumento apresentar desvios frequentes ou inconsistências nas medições, pode ser necessário aumentar a frequência de calibração para garantir que ele continue a operar dentro das especificações. Monitorar o desempenho do instrumento ao longo do tempo pode ajudar a identificar tendências e determinar se ajustes na frequência de calibração são necessários.
As recomendações do fabricante também são um guia importante para a frequência de calibração. Muitos fabricantes fornecem diretrizes específicas sobre a periodicidade de calibração para seus instrumentos, com base em testes e análises de desempenho. É fundamental seguir essas recomendações, pois os fabricantes têm conhecimento profundo sobre as características e limitações de seus produtos. Ignorar essas diretrizes pode resultar em medições imprecisas e comprometer a qualidade do processo.
Outra prática recomendada é a realização de calibrações adicionais sempre que um instrumento for submetido a condições extremas, como mudanças bruscas de temperatura, impactos físicos ou manutenção. Essas situações podem afetar a precisão do instrumento e, portanto, uma calibração deve ser realizada para garantir que ele esteja funcionando corretamente após tais eventos.
Além da calibração regular, é importante que as empresas mantenham um registro detalhado das calibrações realizadas, incluindo datas, resultados e ajustes feitos. Essa documentação é essencial para garantir a rastreabilidade e a conformidade com normas e regulamentos. Além disso, um histórico de calibração pode ajudar a identificar padrões de desempenho e a tomar decisões informadas sobre a frequência de calibração no futuro.
Em resumo, a frequência recomendada para a calibração de instrumentos RBC varia de acordo com a criticidade da aplicação, as condições de operação, o histórico de desempenho do instrumento e as recomendações do fabricante. Instrumentos utilizados em ambientes rigorosos ou que desempenham um papel crítico na segurança e na qualidade do produto devem ser calibrados com mais frequência, enquanto instrumentos em condições controladas podem ter uma frequência de calibração mais espaçada. A adoção de boas práticas de documentação e monitoramento do desempenho dos instrumentos é fundamental para garantir a precisão das medições e a qualidade dos processos industriais.
Erros Comuns na Calibração de Instrumentos RBC e Como Evitá-los
A calibração de instrumentos RBC (Reação de Balanço de Carga) é um processo crítico para garantir a precisão e a confiabilidade das medições em diversas aplicações industriais. No entanto, existem erros comuns que podem ocorrer durante a calibração, comprometendo a eficácia do processo e resultando em medições imprecisas. Neste artigo, discutiremos alguns desses erros e forneceremos orientações sobre como evitá-los, garantindo que a calibração seja realizada de maneira eficaz.
Um dos erros mais frequentes na calibração de instrumentos RBC é a falta de um padrão de referência adequado. A calibração deve ser realizada em comparação com um padrão que tenha uma precisão superior ao instrumento em teste. Se o padrão de referência não for confiável ou não atender às especificações necessárias, os resultados da calibração podem ser comprometidos. Para evitar esse erro, é fundamental utilizar padrões de referência que sejam rastreáveis a organismos de normalização reconhecidos e que estejam em conformidade com as normas aplicáveis.
Outro erro comum é a calibração em condições inadequadas. A temperatura, a umidade e a pressão atmosférica podem afetar significativamente o desempenho dos instrumentos de medição. Realizar a calibração em um ambiente que não esteja controlado pode levar a resultados imprecisos. Para evitar esse problema, é importante realizar a calibração em um ambiente controlado, onde as condições sejam mantidas dentro dos limites especificados pelo fabricante do instrumento. Além disso, é recomendável que a calibração seja realizada em um local que minimize a interferência de vibrações e campos eletromagnéticos.
A falta de treinamento adequado dos profissionais responsáveis pela calibração também é um erro que pode comprometer a precisão do processo. A calibração requer conhecimento técnico e experiência para garantir que os instrumentos sejam ajustados corretamente. Profissionais não treinados podem cometer erros ao interpretar os resultados ou ao realizar os ajustes necessários. Para evitar esse problema, as empresas devem investir em treinamento contínuo para suas equipes, garantindo que os profissionais estejam atualizados sobre as melhores práticas e procedimentos de calibração. Além disso, considerar a contratação de uma empresa de calibração de instrumentos de medição pode ser uma solução eficaz para garantir que a calibração seja realizada por especialistas qualificados.
Outro erro comum é a falta de documentação adequada durante o processo de calibração. A documentação é essencial para garantir a rastreabilidade e a conformidade com normas e regulamentos. A ausência de registros detalhados pode dificultar a identificação de problemas e a realização de auditorias. Para evitar esse erro, as empresas devem estabelecer um sistema de documentação que inclua informações sobre as calibrações realizadas, os resultados obtidos e os ajustes feitos. Essa documentação deve ser mantida de forma organizada e acessível para consultas futuras.
A calibração em intervalos inadequados também é um erro que pode comprometer a precisão das medições. Realizar calibrações com muita frequência pode resultar em custos desnecessários, enquanto calibrações muito espaçadas podem levar a desvios significativos nas medições. Para evitar esse problema, as empresas devem estabelecer um cronograma de calibração baseado nas recomendações do fabricante, na criticidade da aplicação e nas condições de operação. Monitorar o desempenho dos instrumentos ao longo do tempo pode ajudar a ajustar a frequência de calibração conforme necessário.
Além disso, a falta de verificação dos resultados após a calibração é um erro que pode passar despercebido. Após a calibração, é fundamental realizar testes de verificação para garantir que o instrumento esteja funcionando corretamente e que as medições estejam dentro das especificações. Ignorar essa etapa pode resultar em instrumentos que não estão operando de maneira precisa, comprometendo a qualidade do processo. Para evitar esse erro, as empresas devem implementar procedimentos de verificação que incluam testes regulares e a comparação dos resultados com padrões de referência.
Por fim, a resistência a mudanças e a falta de atualização dos procedimentos de calibração também podem ser considerados erros comuns. À medida que novas tecnologias e métodos de calibração são desenvolvidos, é importante que as empresas estejam dispostas a revisar e atualizar seus procedimentos. A resistência a mudanças pode levar a práticas obsoletas que não atendem mais às necessidades do mercado. Para evitar esse problema, as empresas devem promover uma cultura de melhoria contínua, incentivando a equipe a buscar novas soluções e a adotar as melhores práticas de calibração.
Em resumo, os erros comuns na calibração de instrumentos RBC incluem a falta de um padrão de referência adequado, a calibração em condições inadequadas, a falta de treinamento dos profissionais, a ausência de documentação, a calibração em intervalos inadequados, a falta de verificação dos resultados e a resistência a mudanças. Ao identificar e evitar esses erros, as empresas podem garantir que a calibração de seus instrumentos seja realizada de maneira eficaz, resultando em medições precisas e confiáveis que são essenciais para a qualidade e a segurança dos processos industriais.
Em conclusão, a calibração de instrumentos RBC é uma prática essencial que não apenas assegura a precisão das medições, mas também contribui para a segurança e a qualidade dos processos em diversas indústrias. A compreensão da importância da calibração, dos métodos adequados, da frequência recomendada e dos erros comuns a serem evitados é crucial para qualquer organização que busca manter altos padrões de qualidade. Investir em calibração regular e em profissionais qualificados, além de seguir as melhores práticas, garantirá que os instrumentos operem de maneira eficaz, resultando em dados confiáveis e em um desempenho otimizado. Assim, a calibração se torna um pilar fundamental para o sucesso e a sustentabilidade das operações industriais.