Calibração de instrumentos de medição para garantir precisão e confiabilidade
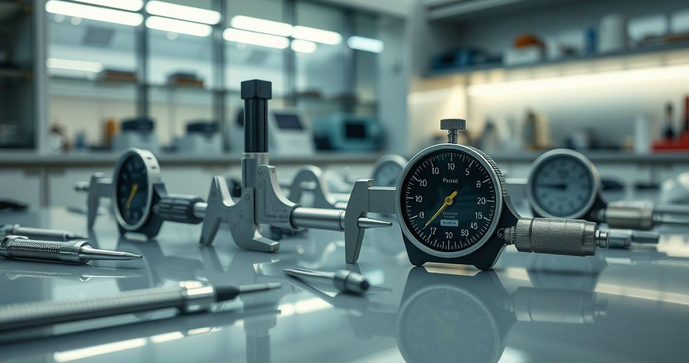
Por: Rafael - 26 de Fevereiro de 2025
A calibração de instrumentos de medição é um processo fundamental para garantir a precisão e a confiabilidade dos resultados obtidos em diversas aplicações, desde laboratórios até indústrias. Com a crescente demanda por qualidade e conformidade em processos produtivos, entender a importância da calibração se torna essencial. Neste artigo, abordaremos os métodos, a frequência recomendada e os erros comuns relacionados à calibração de instrumentos de medição, proporcionando uma visão abrangente sobre o tema.
Importância da Calibração de Instrumentos de Medição na Indústria
A calibração de instrumentos de medição é um aspecto crucial na indústria, pois assegura que os equipamentos utilizados para medir variáveis como pressão, temperatura, vazão e outros parâmetros operem com precisão. A precisão das medições é vital para a qualidade dos produtos, a segurança dos processos e a conformidade com normas regulatórias. Neste contexto, a calibração não é apenas uma prática recomendada, mas uma necessidade para garantir a eficiência e a eficácia das operações industriais.
Um dos principais motivos para a calibração de instrumentos de medição é a minimização de erros. Instrumentos que não são calibrados regularmente podem apresentar desvios que afetam a qualidade dos dados coletados. Esses desvios podem resultar em decisões erradas, que podem comprometer a produção e a segurança. Por exemplo, em uma linha de produção de alimentos, a medição incorreta da temperatura pode levar a produtos não seguros para o consumo, resultando em recalls e danos à reputação da empresa.
Além disso, a calibração é fundamental para a conformidade com normas e regulamentos. Muitas indústrias, como a farmacêutica e a alimentícia, estão sujeitas a rigorosos padrões de qualidade e segurança. A calibração regular dos instrumentos de medição é uma exigência para garantir que os processos atendam a essas normas. A falta de calibração pode resultar em penalidades, multas e até mesmo a suspensão das operações. Portanto, manter um programa de calibração eficaz é essencial para evitar problemas legais e garantir a continuidade dos negócios.
A calibração também desempenha um papel importante na otimização de processos. Instrumentos de medição precisos permitem que as empresas monitorem e ajustem seus processos em tempo real, resultando em maior eficiência e redução de desperdícios. Por exemplo, em um sistema de controle de vazão, um medidor de vazão ultrassônico calibrado corretamente pode ajudar a garantir que a quantidade de líquido utilizada em um processo seja a ideal, evitando excessos que podem levar a custos desnecessários e impactos ambientais negativos.
Outro aspecto a ser considerado é a durabilidade dos instrumentos de medição. A calibração regular não apenas assegura a precisão, mas também pode prolongar a vida útil dos equipamentos. Instrumentos que operam fora das especificações podem sofrer desgaste prematuro, resultando em custos adicionais com manutenção e substituição. Ao realizar a calibração de forma sistemática, as empresas podem identificar problemas antes que se tornem críticos, economizando tempo e recursos a longo prazo.
Além disso, a calibração contribui para a confiança nas medições. Quando os operadores e gerentes sabem que os instrumentos estão calibrados e funcionando corretamente, eles podem tomar decisões informadas com base em dados confiáveis. Isso é especialmente importante em ambientes industriais onde a precisão é vital para a segurança e a eficiência. A confiança nas medições também é um fator chave para a melhoria contínua, pois permite que as empresas analisem seu desempenho e implementem melhorias com base em dados concretos.
Por fim, a calibração de instrumentos de medição é uma prática que promove a cultura de qualidade dentro das organizações. Ao priorizar a calibração, as empresas demonstram seu compromisso com a excelência e a melhoria contínua. Isso não apenas melhora a qualidade dos produtos e serviços, mas também pode aumentar a satisfação do cliente e a lealdade à marca. Em um mercado competitivo, a reputação de uma empresa pode ser um diferencial significativo, e a calibração é uma parte fundamental dessa equação.
Em resumo, a calibração de instrumentos de medição na indústria é de extrema importância para garantir a precisão, a conformidade, a otimização de processos, a durabilidade dos equipamentos e a confiança nas medições. As empresas que investem em programas de calibração eficazes não apenas protegem sua operação, mas também se posicionam para o sucesso a longo prazo. Portanto, é essencial que as indústrias reconheçam a importância da calibração e implementem práticas adequadas para garantir que seus instrumentos de medição estejam sempre em conformidade e operando com precisão.
Métodos Comuns de Calibração de Instrumentos
A calibração de instrumentos de medição é um processo essencial para garantir a precisão e a confiabilidade dos dados coletados em diversas aplicações industriais e laboratoriais. Existem vários métodos de calibração que podem ser utilizados, dependendo do tipo de instrumento, da aplicação e dos requisitos específicos de cada setor. Neste artigo, abordaremos alguns dos métodos comuns de calibração de instrumentos, destacando suas características e aplicações.
Um dos métodos mais tradicionais de calibração é a calibração por comparação. Este método envolve a comparação do instrumento a ser calibrado com um padrão de referência conhecido e rastreável. O instrumento de referência deve ter uma precisão superior à do instrumento em teste. Durante o processo, o operador realiza medições com ambos os instrumentos nas mesmas condições e compara os resultados. As diferenças observadas são então usadas para ajustar o instrumento em teste, garantindo que suas medições estejam alinhadas com o padrão de referência. Este método é amplamente utilizado em laboratórios e indústrias, pois é relativamente simples e eficaz.
Outro método comum é a calibração por ajuste. Neste caso, o instrumento é ajustado diretamente para que suas medições correspondam a um padrão conhecido. Esse método é frequentemente utilizado em instrumentos que possuem um mecanismo de ajuste interno, como manômetros e termômetros. O operador realiza medições em pontos específicos e ajusta o instrumento conforme necessário. A calibração por ajuste é particularmente útil quando se deseja garantir que o instrumento opere dentro de uma faixa específica de tolerância.
A calibração por simulação é um método que utiliza um dispositivo de simulação para gerar sinais de entrada que imitam as condições reais de operação do instrumento. Este método é especialmente útil para instrumentos eletrônicos, como multímetros e osciloscópios. O dispositivo de simulação fornece sinais de entrada em diferentes níveis, permitindo que o operador verifique a resposta do instrumento em teste. A calibração por simulação é eficaz para identificar não apenas desvios, mas também problemas de linearidade e histerese, que podem afetar a precisão das medições.
Além disso, a calibração em campo é um método que envolve a calibração de instrumentos diretamente no local de operação. Este método é frequentemente utilizado para instrumentos que não podem ser facilmente removidos ou que precisam ser calibrados em condições reais de uso. A calibração em campo pode ser realizada por técnicos especializados que utilizam equipamentos de referência portáteis. Embora esse método possa ser mais desafiador devido a variáveis ambientais, ele é essencial para garantir que os instrumentos estejam funcionando corretamente nas condições em que serão utilizados.
Outro método importante é a calibração por transferência. Este método é utilizado quando não é possível acessar um padrão de referência diretamente. Em vez disso, um instrumento que já foi calibrado e é considerado confiável é utilizado para calibrar outro instrumento. A calibração por transferência é comum em ambientes onde os padrões de referência não estão disponíveis ou onde a calibração em campo é necessária. No entanto, é importante garantir que o instrumento de transferência também esteja calibrado e rastreável para evitar a propagação de erros.
As empresas de calibração de equipamentos desempenham um papel fundamental na implementação desses métodos. Elas oferecem serviços especializados que garantem que os instrumentos de medição sejam calibrados de acordo com as normas e regulamentos aplicáveis. Essas empresas possuem equipamentos de referência de alta precisão e técnicos qualificados que podem realizar calibrações em laboratório ou em campo, dependendo das necessidades do cliente.
Além dos métodos mencionados, a calibração também pode ser realizada utilizando técnicas de software. Com o avanço da tecnologia, muitos instrumentos modernos vêm equipados com recursos de calibração automática que utilizam algoritmos para ajustar as medições com base em dados de referência. Esses sistemas podem simplificar o processo de calibração e reduzir a possibilidade de erro humano. No entanto, é importante que esses sistemas sejam verificados regularmente para garantir sua precisão e confiabilidade.
Por fim, a escolha do método de calibração adequado depende de vários fatores, incluindo o tipo de instrumento, a aplicação, a precisão necessária e as condições de operação. É fundamental que as empresas desenvolvam um plano de calibração que inclua a frequência das calibrações, os métodos a serem utilizados e a documentação necessária para garantir a conformidade com as normas e regulamentos aplicáveis. A calibração regular não apenas assegura a precisão das medições, mas também contribui para a eficiência operacional e a segurança dos processos industriais.
Em resumo, os métodos comuns de calibração de instrumentos incluem calibração por comparação, ajuste, simulação, em campo e transferência. Cada método possui suas características e aplicações específicas, e a escolha do método adequado é crucial para garantir a precisão e a confiabilidade das medições. As empresas de calibração desempenham um papel vital nesse processo, oferecendo serviços especializados que ajudam a manter os instrumentos em conformidade e funcionando corretamente.
Frequência Recomendada para Calibração de Instrumentos de Medição
A calibração de instrumentos de medição é um processo essencial para garantir a precisão e a confiabilidade dos dados coletados em diversas aplicações industriais e laboratoriais. No entanto, a eficácia desse processo depende não apenas da qualidade da calibração em si, mas também da frequência com que ela é realizada. Neste artigo, discutiremos a frequência recomendada para a calibração de instrumentos de medição, considerando fatores que influenciam essa periodicidade e a importância de manter um cronograma adequado.
A frequência de calibração pode variar significativamente dependendo do tipo de instrumento, da aplicação, das condições de operação e das exigências regulatórias. Em geral, a calibração deve ser realizada em intervalos regulares para garantir que os instrumentos permaneçam dentro das especificações de precisão. Para muitos instrumentos, como termômetros, manômetros e medidores de vazão, a calibração é recomendada a cada 6 a 12 meses. No entanto, essa frequência pode ser ajustada com base em fatores específicos.
Um dos principais fatores a considerar ao determinar a frequência de calibração é a criticidade do instrumento para o processo em que está sendo utilizado. Instrumentos que desempenham um papel crucial na segurança ou na qualidade do produto devem ser calibrados com mais frequência. Por exemplo, em indústrias farmacêuticas e alimentícias, onde a precisão das medições é vital para garantir a segurança do consumidor, a calibração pode ser necessária a cada três meses ou até mensalmente. A calibração frequente ajuda a evitar desvios que podem resultar em produtos não conformes e, consequentemente, em recalls e danos à reputação da empresa.
Outro fator a ser considerado é a intensidade de uso do instrumento. Instrumentos que são utilizados em ambientes de alta demanda ou que operam em condições adversas, como temperaturas extremas ou ambientes corrosivos, podem exigir calibrações mais frequentes. O desgaste e a degradação podem ocorrer mais rapidamente nessas condições, afetando a precisão das medições. Portanto, é importante monitorar o desempenho do instrumento e ajustar a frequência de calibração conforme necessário.
Além disso, a frequência de calibração pode ser influenciada por mudanças nas condições de operação. Se um instrumento for movido para um novo local, utilizado em um novo processo ou exposto a diferentes condições ambientais, é recomendável realizar uma calibração antes de retomar o uso. Mudanças nas condições podem afetar a precisão do instrumento, e a calibração ajuda a garantir que ele esteja funcionando corretamente nas novas circunstâncias.
As normas e regulamentos aplicáveis também desempenham um papel importante na determinação da frequência de calibração. Muitas indústrias estão sujeitas a regulamentações que exigem calibrações em intervalos específicos. Por exemplo, a ISO 9001 e outras normas de qualidade podem exigir que as empresas mantenham um cronograma de calibração documentado. É fundamental que as organizações estejam cientes das exigências regulatórias que se aplicam a seus processos e instrumentos e que sigam essas diretrizes para garantir a conformidade.
Além da calibração regular, é importante realizar verificações periódicas entre as calibrações. Essas verificações podem incluir testes simples para garantir que o instrumento esteja funcionando corretamente e dentro das especificações. Se uma verificação indicar que o instrumento está fora de especificação, uma calibração deve ser realizada imediatamente, independentemente do cronograma regular. Isso ajuda a garantir que os instrumentos permaneçam precisos e confiáveis ao longo do tempo.
As empresas devem desenvolver um plano de calibração que inclua a frequência recomendada para cada tipo de instrumento, levando em consideração os fatores mencionados. Esse plano deve ser documentado e revisado regularmente para garantir que continue a atender às necessidades da organização. Além disso, é importante que as empresas mantenham registros detalhados de todas as calibrações realizadas, incluindo datas, resultados e quaisquer ajustes feitos. Esses registros são essenciais para garantir a conformidade com as normas e regulamentos e para fornecer uma trilha de auditoria em caso de inspeções.
Em resumo, a frequência recomendada para a calibração de instrumentos de medição varia de acordo com o tipo de instrumento, a criticidade da aplicação, as condições de operação e as exigências regulatórias. A calibração deve ser realizada em intervalos regulares, com ajustes baseados em fatores específicos, como intensidade de uso e mudanças nas condições de operação. Manter um cronograma de calibração adequado é fundamental para garantir a precisão e a confiabilidade das medições, contribuindo para a eficiência operacional e a segurança dos processos industriais.
Erros Comuns na Calibração e Como Evitá-los
A calibração de instrumentos de medição é um processo crítico para garantir a precisão e a confiabilidade das medições em diversas aplicações industriais e laboratoriais. No entanto, existem erros comuns que podem ocorrer durante o processo de calibração, comprometendo a eficácia e a precisão dos resultados. Neste artigo, discutiremos alguns desses erros e forneceremos orientações sobre como evitá-los, garantindo que a calibração seja realizada de maneira eficaz.
Um dos erros mais frequentes na calibração é a falta de um padrão de referência adequado. A calibração deve ser realizada em comparação com um padrão que seja rastreável a um laboratório nacional de metrologia. Se o padrão de referência não for adequado ou não estiver calibrado, os resultados da calibração podem ser imprecisos. Para evitar esse erro, é fundamental que as empresas utilizem padrões de referência que sejam reconhecidos e que tenham sua calibração verificada regularmente. Além disso, é importante que os técnicos responsáveis pela calibração estejam cientes da importância de utilizar padrões adequados.
Outro erro comum é a falta de condições ambientais controladas durante o processo de calibração. A temperatura, a umidade e a pressão atmosférica podem afetar significativamente as medições. Se a calibração for realizada em condições ambientais inadequadas, os resultados podem ser comprometidos. Para evitar esse problema, as calibrações devem ser realizadas em ambientes controlados, onde as condições possam ser monitoradas e mantidas dentro de limites aceitáveis. Isso é especialmente importante para instrumentos sensíveis, como balanças e termômetros.
A calibração inadequada do instrumento em teste também é um erro que pode ocorrer. Isso pode acontecer quando o operador não segue corretamente os procedimentos de calibração ou não realiza os ajustes necessários. Para evitar esse erro, é essencial que os técnicos sejam devidamente treinados e que sigam rigorosamente os procedimentos estabelecidos. Além disso, a documentação dos procedimentos de calibração deve ser clara e acessível, garantindo que todos os envolvidos no processo compreendam as etapas necessárias.
Outro erro que pode ocorrer é a falta de verificação da estabilidade do instrumento antes da calibração. Instrumentos que não estão estáveis podem apresentar resultados imprecisos. Antes de iniciar o processo de calibração, é importante verificar se o instrumento está em condições adequadas de funcionamento. Isso pode incluir a realização de testes preliminares para garantir que o instrumento esteja operando corretamente. Se o instrumento não estiver estável, a calibração deve ser adiada até que o problema seja resolvido.
A falta de documentação adequada também é um erro comum na calibração. Registros detalhados das calibrações realizadas, incluindo datas, resultados e ajustes feitos, são essenciais para garantir a conformidade com as normas e regulamentos. A falta de documentação pode levar a problemas durante auditorias e inspeções. Para evitar esse erro, as empresas devem implementar um sistema de gerenciamento de documentos que permita o registro e o acompanhamento de todas as calibrações realizadas. Isso não apenas ajuda a garantir a conformidade, mas também fornece uma trilha de auditoria que pode ser útil em caso de disputas ou questionamentos.
Além disso, a escolha inadequada do método de calibração pode resultar em erros. Cada instrumento pode exigir um método específico de calibração, e a utilização de um método inadequado pode comprometer a precisão dos resultados. Para evitar esse erro, é importante que as empresas conheçam as especificações de cada instrumento e escolham o método de calibração apropriado. Consultar especialistas ou empresa de calibração de instrumentos de medição pode ser uma boa prática para garantir que os métodos utilizados sejam os mais adequados.
Outro erro que pode ocorrer é a falta de manutenção regular dos instrumentos. Instrumentos que não são mantidos adequadamente podem apresentar desvios que afetam a precisão das medições. A manutenção preventiva deve ser parte integrante do programa de calibração, garantindo que os instrumentos estejam sempre em boas condições de funcionamento. Isso inclui a limpeza regular, a verificação de componentes e a substituição de peças desgastadas.
Por fim, a falta de um cronograma de calibração pode levar a erros. A calibração deve ser realizada em intervalos regulares, e a falta de um cronograma pode resultar em calibrações atrasadas ou esquecidas. Para evitar esse problema, as empresas devem desenvolver um plano de calibração que inclua a frequência recomendada para cada tipo de instrumento, levando em consideração fatores como a criticidade da aplicação e as condições de operação. Manter um cronograma atualizado e monitorar as calibrações programadas é essencial para garantir a precisão contínua dos instrumentos.
Em resumo, os erros comuns na calibração de instrumentos de medição incluem a falta de um padrão de referência adequado, condições ambientais inadequadas, calibração inadequada, falta de verificação da estabilidade do instrumento, falta de documentação, escolha inadequada do método de calibração, falta de manutenção regular e ausência de um cronograma de calibração. Ao estar ciente desses erros e implementar práticas adequadas para evitá-los, as empresas podem garantir que seus instrumentos de medição permaneçam precisos e confiáveis, contribuindo para a eficiência e a segurança de suas operações.
Em conclusão, a calibração de instrumentos de medição é uma prática indispensável para assegurar a qualidade e a precisão em diversos setores. A compreensão dos métodos de calibração, a definição de uma frequência adequada e a identificação de erros comuns são passos cruciais para otimizar esse processo. Ao implementar um programa de calibração eficaz, as empresas não apenas garantem a conformidade com normas e regulamentos, mas também promovem a eficiência operacional e a segurança em suas operações. Investir na calibração adequada é, portanto, um compromisso com a excelência e a melhoria contínua, refletindo diretamente na qualidade dos produtos e serviços oferecidos.