Calibração de Equipamentos de Medição: Garantindo a Precisão e Confiabilidade
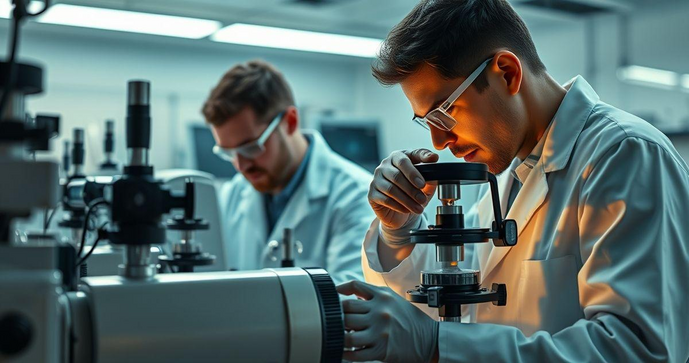
Por: Rafael - 21 de Fevereiro de 2025
A calibração de equipamentos de medição é um processo fundamental para garantir a precisão e a confiabilidade dos resultados obtidos em diversas aplicações, desde laboratórios até indústrias. Com a crescente demanda por qualidade e conformidade em processos produtivos, entender a importância da calibração e os métodos disponíveis se torna essencial. Neste artigo, abordaremos os principais aspectos relacionados à calibração de equipamentos de medição, incluindo sua importância, métodos comuns, frequência recomendada e erros a serem evitados.
Importância da Calibração de Equipamentos de Medição
A calibração de equipamentos de medição é um aspecto crucial em diversos setores, incluindo indústria, laboratórios e serviços de saúde. Este processo assegura que os instrumentos de medição estejam funcionando corretamente e fornecendo resultados precisos e confiáveis. A precisão nas medições é vital, pois qualquer erro pode levar a consequências significativas, como falhas em processos produtivos, comprometimento da qualidade do produto e até riscos à segurança.
Um dos principais motivos para a calibração é a necessidade de conformidade com normas e regulamentos. Muitas indústrias são obrigadas a seguir padrões específicos que garantem a qualidade e a segurança dos produtos. A calibração regular dos equipamentos de medição é uma exigência para atender a essas normas, evitando penalidades e garantindo a confiança dos consumidores. Por exemplo, em setores como farmacêutico e alimentício, a precisão nas medições é essencial para garantir que os produtos atendam aos requisitos de segurança e eficácia.
Além disso, a calibração ajuda a prolongar a vida útil dos equipamentos. Instrumentos que não são calibrados regularmente podem sofrer desgastes e danos, resultando em falhas e necessidade de reparos ou substituições mais frequentes. A manutenção preventiva, que inclui a calibração, pode reduzir custos operacionais a longo prazo, uma vez que evita interrupções na produção e a compra de novos equipamentos.
A calibração também é fundamental para a melhoria contínua dos processos. Ao garantir que os equipamentos de medição estejam funcionando corretamente, as empresas podem identificar áreas de melhoria e otimizar suas operações. Por exemplo, em um processo de fabricação, medições precisas podem ajudar a ajustar parâmetros de produção, resultando em maior eficiência e redução de desperdícios.
Outro aspecto importante é a confiança nas medições. Quando os resultados são precisos e confiáveis, as decisões tomadas com base nesses dados são mais seguras. Isso é especialmente relevante em setores críticos, como saúde e segurança, onde medições imprecisas podem ter consequências graves. A calibração regular dos equipamentos de medição garante que os profissionais possam confiar nos dados que estão utilizando para tomar decisões informadas.
Além disso, a calibração é essencial para a rastreabilidade das medições. Em muitos casos, é necessário que as medições possam ser rastreadas até padrões nacionais ou internacionais. A calibração fornece a documentação necessária para garantir que os resultados possam ser verificados e validados. Isso é particularmente importante em auditorias e inspeções, onde a conformidade com os padrões de qualidade é avaliada.
Um exemplo prático da importância da calibração pode ser observado no uso de Medidor de vazão ultrassônico em aplicações industriais. Esses dispositivos são utilizados para medir a vazão de líquidos e gases, e sua precisão é fundamental para o controle de processos. Se um medidor de vazão não estiver calibrado corretamente, pode resultar em medições imprecisas, levando a desperdícios de recursos e custos adicionais. Portanto, a calibração regular é essencial para garantir que esses instrumentos funcionem de maneira eficaz e eficiente.
Além dos benefícios diretos, a calibração também pode impactar a reputação da empresa. Organizações que demonstram compromisso com a qualidade e a precisão em suas operações tendem a ganhar a confiança de seus clientes e parceiros. Isso pode resultar em uma vantagem competitiva no mercado, onde a qualidade é um diferencial importante. A calibração, portanto, não é apenas uma questão de conformidade, mas também uma estratégia de negócios que pode influenciar o sucesso a longo prazo.
Por fim, a calibração de equipamentos de medição é um investimento que traz retornos significativos. Embora possa haver custos associados à calibração, os benefícios superam amplamente esses custos. A precisão nas medições, a conformidade com normas, a melhoria contínua dos processos e a confiança nas decisões são apenas alguns dos aspectos que tornam a calibração um componente essencial da operação de qualquer organização que dependa de medições precisas.
Em resumo, a calibração de equipamentos de medição é vital para garantir a precisão, a confiabilidade e a conformidade em diversos setores. Este processo não apenas ajuda a evitar erros e falhas, mas também contribui para a eficiência operacional e a confiança nas medições. Investir na calibração regular dos equipamentos é uma prática que traz benefícios significativos e deve ser uma prioridade para todas as organizações que buscam excelência em suas operações.
Métodos Comuns de Calibração
A calibração é um processo essencial para garantir a precisão e a confiabilidade dos equipamentos de medição. Existem diversos métodos de calibração que podem ser aplicados, dependendo do tipo de equipamento, da aplicação e dos requisitos específicos de cada setor. Neste artigo, abordaremos alguns dos métodos comuns de calibração, suas características e quando cada um deles deve ser utilizado.
Um dos métodos mais utilizados é a calibração por comparação. Este método envolve a comparação do equipamento a ser calibrado com um padrão de referência que possui uma precisão conhecida. O equipamento de referência deve ser rastreável a padrões nacionais ou internacionais, garantindo a confiabilidade dos resultados. Durante o processo, o equipamento em teste é submetido a medições em condições controladas, e os resultados são comparados com os valores do padrão. Essa abordagem é amplamente utilizada em laboratórios e indústrias, pois permite identificar desvios e ajustar o equipamento conforme necessário.
Outro método comum é a calibração por ajuste. Neste caso, o equipamento é ajustado diretamente para atender a um padrão específico. Isso é feito quando o equipamento apresenta desvios significativos em relação ao padrão de referência. A calibração por ajuste é frequentemente utilizada em instrumentos que não podem ser simplesmente comparados, como alguns tipos de sensores e medidores. Após o ajuste, o equipamento é testado novamente para garantir que agora está dentro das especificações desejadas.
A calibração em campo é um método que se tornou cada vez mais popular, especialmente em aplicações industriais. Este método envolve a calibração do equipamento no local onde ele será utilizado, em vez de enviá-lo para um laboratório. A calibração em campo é vantajosa porque permite que os técnicos realizem ajustes e verificações em condições reais de operação. Isso é especialmente importante para equipamentos que podem ser afetados por fatores ambientais, como temperatura e pressão. Muitas Empresas de calibração de equipamentos oferecem serviços de calibração em campo, proporcionando conveniência e eficiência para os clientes.
Outro método relevante é a calibração por simulação. Este método é utilizado principalmente para equipamentos que não podem ser calibrados diretamente, como alguns instrumentos eletrônicos. A calibração por simulação envolve a aplicação de sinais de entrada conhecidos ao equipamento e a medição da saída correspondente. Isso permite que os técnicos verifiquem se o equipamento está respondendo corretamente a diferentes condições de entrada. A calibração por simulação é frequentemente utilizada em laboratórios de eletrônica e em indústrias que dependem de medições eletrônicas precisas.
A calibração por transferência é um método que envolve o uso de um equipamento intermediário para transferir a calibração de um instrumento para outro. Este método é útil quando não é prático ou possível calibrar diretamente um equipamento. Por exemplo, um medidor de pressão pode ser calibrado usando um manômetro de referência, que já foi calibrado em um laboratório. A calibração por transferência é uma abordagem eficiente, especialmente em ambientes onde o tempo e os recursos são limitados.
Além dos métodos mencionados, a calibração também pode ser realizada utilizando padrões de referência. Esses padrões são instrumentos que possuem uma precisão conhecida e são utilizados para verificar e ajustar outros equipamentos. A calibração com padrões de referência é uma prática comum em laboratórios de metrologia e é essencial para garantir a rastreabilidade das medições. Os padrões devem ser calibrados regularmente para garantir que permaneçam precisos ao longo do tempo.
Outro aspecto importante a considerar na calibração é a frequência com que ela deve ser realizada. A frequência de calibração pode variar dependendo do tipo de equipamento, da aplicação e das condições de uso. Equipamentos que são utilizados em ambientes críticos ou que operam em condições extremas podem exigir calibrações mais frequentes. Por outro lado, equipamentos que são utilizados em condições controladas podem ter intervalos de calibração mais longos. É fundamental seguir as recomendações do fabricante e as normas aplicáveis para determinar a frequência adequada de calibração.
Por fim, a documentação é um componente essencial do processo de calibração. Todos os resultados de calibração devem ser registrados e mantidos em arquivos para garantir a rastreabilidade e a conformidade com as normas. A documentação deve incluir informações sobre o equipamento, os métodos utilizados, os resultados obtidos e quaisquer ajustes realizados. Isso não apenas ajuda a garantir a qualidade, mas também é fundamental para auditorias e inspeções.
Em resumo, existem diversos métodos de calibração que podem ser aplicados, cada um com suas características e aplicações específicas. A escolha do método adequado depende do tipo de equipamento, das condições de uso e dos requisitos de precisão. A calibração regular e adequada é essencial para garantir a confiabilidade das medições e a conformidade com as normas, contribuindo para a eficiência e a qualidade em diversos setores.
Frequência Recomendada para Calibração
A calibração de equipamentos de medição é um processo vital para garantir a precisão e a confiabilidade dos resultados obtidos em diversas aplicações. No entanto, a eficácia desse processo depende não apenas da qualidade da calibração em si, mas também da frequência com que ela é realizada. A frequência recomendada para calibração pode variar significativamente de acordo com o tipo de equipamento, a aplicação, as condições de uso e as normas regulatórias aplicáveis. Neste artigo, discutiremos os fatores que influenciam a frequência de calibração e forneceremos orientações sobre como determinar a periodicidade ideal para diferentes tipos de equipamentos.
Um dos principais fatores a considerar ao determinar a frequência de calibração é o tipo de equipamento. Equipamentos que são utilizados em ambientes críticos ou que realizam medições de alta precisão, como um Medidor de vazão , geralmente requerem calibrações mais frequentes. Isso se deve ao fato de que pequenas variações nas medições podem ter um impacto significativo na qualidade do produto ou na segurança do processo. Por outro lado, equipamentos que operam em condições menos exigentes podem ter intervalos de calibração mais longos.
Outro aspecto importante a considerar é a intensidade de uso do equipamento. Equipamentos que são utilizados com frequência ou que estão sujeitos a condições adversas, como vibrações, temperaturas extremas ou umidade, podem exigir calibrações mais regulares. Por exemplo, um medidor de pressão que é utilizado em um ambiente industrial pode sofrer desgastes mais rapidamente do que um medidor que é usado em um laboratório controlado. Portanto, a frequência de calibração deve ser ajustada com base nas condições reais de operação.
As recomendações do fabricante também desempenham um papel crucial na determinação da frequência de calibração. Os fabricantes geralmente fornecem diretrizes específicas sobre a periodicidade de calibração para seus equipamentos, com base em testes e experiências anteriores. É fundamental seguir essas recomendações, pois elas são projetadas para garantir o desempenho ideal do equipamento e a conformidade com as normas aplicáveis. Ignorar essas diretrizes pode resultar em medições imprecisas e em problemas de conformidade.
Além disso, as normas e regulamentos do setor podem influenciar a frequência de calibração. Em muitos setores, como farmacêutico, alimentício e de saúde, existem requisitos rigorosos que determinam a periodicidade de calibração dos equipamentos de medição. Essas normas são estabelecidas para garantir a segurança e a qualidade dos produtos e serviços oferecidos. Portanto, é essencial estar ciente das regulamentações aplicáveis ao seu setor e garantir que a frequência de calibração esteja em conformidade com essas exigências.
Um método eficaz para determinar a frequência de calibração é realizar uma análise de risco. Essa abordagem envolve a avaliação dos riscos associados a medições imprecisas e a determinação da frequência de calibração necessária para mitigar esses riscos. Por exemplo, se um equipamento é responsável por medições críticas que afetam a segurança do produto, pode ser necessário calibrá-lo com mais frequência do que um equipamento que não tem um impacto tão significativo. A análise de risco pode ajudar a priorizar os equipamentos que exigem calibrações mais frequentes e a alocar recursos de forma eficaz.
Além disso, a frequência de calibração pode ser ajustada com base em resultados anteriores. Se um equipamento apresentar desvios significativos durante a calibração, pode ser um sinal de que a frequência atual não é adequada. Nesse caso, pode ser necessário aumentar a frequência de calibração para garantir que o equipamento permaneça dentro das especificações. Por outro lado, se um equipamento apresentar resultados consistentes e precisos ao longo do tempo, pode ser possível estender o intervalo de calibração.
É importante também considerar a documentação e o registro das calibrações realizadas. Manter um histórico detalhado das calibrações, incluindo datas, resultados e ajustes realizados, pode ajudar a identificar padrões e tendências ao longo do tempo. Essa documentação é essencial para auditorias e inspeções, além de fornecer informações valiosas para a tomada de decisões sobre a frequência de calibração.
Por fim, a formação e a conscientização da equipe que opera e mantém os equipamentos também são fundamentais. Profissionais bem treinados são mais propensos a identificar problemas e a realizar manutenções preventivas, o que pode impactar positivamente a frequência de calibração. Investir em treinamento e capacitação pode resultar em uma operação mais eficiente e em medições mais precisas.
Em resumo, a frequência recomendada para calibração é um aspecto crítico que deve ser cuidadosamente considerado. Fatores como o tipo de equipamento, as condições de uso, as recomendações do fabricante e as normas regulatórias desempenham um papel importante na determinação da periodicidade ideal. Realizar uma análise de risco e manter uma documentação adequada são práticas que podem ajudar a otimizar a frequência de calibração, garantindo a precisão e a confiabilidade das medições ao longo do tempo.
Erros Comuns na Calibração de Equipamentos
A calibração de equipamentos de medição é um processo essencial para garantir a precisão e a confiabilidade dos resultados obtidos em diversas aplicações. No entanto, existem vários erros que podem ocorrer durante esse processo, comprometendo a eficácia da calibração e, consequentemente, a qualidade das medições. Neste artigo, discutiremos os erros comuns na calibração de equipamentos, suas causas e como evitá-los.
Um dos erros mais frequentes é a falta de um padrão de referência adequado. A calibração deve ser realizada utilizando padrões que sejam rastreáveis a normas nacionais ou internacionais. Quando um padrão de referência não é utilizado ou não possui a precisão necessária, os resultados da calibração podem ser imprecisos. Isso pode levar a medições erradas e a decisões baseadas em dados não confiáveis. Portanto, é fundamental garantir que os padrões utilizados sejam adequados e estejam em conformidade com as especificações necessárias.
Outro erro comum é a calibração em condições inadequadas. A temperatura, a umidade e outras condições ambientais podem afetar significativamente os resultados da calibração. Por exemplo, se um equipamento for calibrado em um ambiente com temperaturas extremas ou alta umidade, isso pode resultar em medições imprecisas. É importante realizar a calibração em condições controladas e apropriadas, conforme recomendado pelo fabricante e pelas normas aplicáveis.
A falta de treinamento adequado dos profissionais que realizam a calibração também é um fator que contribui para erros. A calibração é um processo técnico que requer conhecimento e habilidades específicas. Profissionais não treinados podem cometer erros ao operar os equipamentos, interpretar os resultados ou seguir os procedimentos de calibração. Investir em treinamento e capacitação para a equipe responsável pela calibração é essencial para minimizar esses riscos. Muitas Empresa de calibração de instrumentos de medição oferecem cursos e treinamentos que podem ajudar a melhorar as habilidades da equipe.
Outro erro comum é a falta de documentação adequada durante o processo de calibração. A documentação é fundamental para garantir a rastreabilidade e a conformidade com as normas. Sem registros detalhados, é difícil verificar se a calibração foi realizada corretamente e se os resultados estão dentro das especificações. Além disso, a falta de documentação pode complicar auditorias e inspeções, resultando em penalidades e problemas de conformidade. Portanto, é crucial manter um registro completo de todas as calibrações realizadas, incluindo datas, resultados e ajustes feitos.
A calibração inadequada dos equipamentos também pode ocorrer devido à falta de manutenção preventiva. Equipamentos que não são mantidos adequadamente podem apresentar falhas e desvios que afetam a precisão das medições. A manutenção regular, que inclui limpeza, lubrificação e verificação de componentes, é essencial para garantir que os equipamentos funcionem corretamente. Ignorar a manutenção pode levar a erros durante a calibração e a medições imprecisas.
Além disso, a pressão para realizar calibrações rapidamente pode resultar em erros. Em ambientes industriais, pode haver uma pressão significativa para minimizar o tempo de inatividade dos equipamentos. Isso pode levar a uma calibração apressada, onde os procedimentos não são seguidos corretamente ou os testes não são realizados de forma adequada. É importante equilibrar a necessidade de eficiência com a necessidade de precisão, garantindo que a calibração seja realizada de acordo com os padrões estabelecidos.
Outro erro que pode ocorrer é a falta de verificação pós-calibração. Após a calibração, é fundamental realizar testes para garantir que o equipamento esteja funcionando corretamente e que os resultados estejam dentro das especificações. Ignorar essa etapa pode resultar em problemas não detectados que podem afetar a qualidade das medições. A verificação pós-calibração deve ser uma parte integrante do processo de calibração.
Por fim, a falta de um plano de calibração bem definido pode levar a erros. Um plano de calibração deve incluir a frequência de calibração, os métodos a serem utilizados, os padrões de referência e as responsabilidades da equipe. Sem um plano claro, pode haver confusão sobre quando e como realizar a calibração, resultando em medições imprecisas e problemas de conformidade. É importante desenvolver e seguir um plano de calibração que atenda às necessidades específicas da organização.
Em resumo, a calibração de equipamentos de medição é um processo crítico que deve ser realizado com cuidado e atenção. Erros comuns, como a falta de padrões adequados, condições inadequadas, falta de treinamento, documentação insuficiente, manutenção negligenciada, pressão para realizar calibrações rapidamente, falta de verificação pós-calibração e ausência de um plano de calibração podem comprometer a eficácia do processo. Ao estar ciente desses erros e implementar medidas para evitá-los, as organizações podem garantir medições precisas e confiáveis, contribuindo para a qualidade e a segurança de seus produtos e serviços.
Em conclusão, a calibração de equipamentos de medição é um aspecto crucial que não pode ser negligenciado em qualquer setor que dependa de medições precisas. A compreensão da importância da calibração, aliada ao conhecimento dos métodos adequados, da frequência recomendada e dos erros comuns a serem evitados, é fundamental para garantir a qualidade e a confiabilidade dos resultados. Ao implementar práticas eficazes de calibração, as organizações não apenas atendem às normas e regulamentos, mas também promovem a eficiência operacional e a segurança em seus processos. Investir em calibração é, portanto, um passo essencial para assegurar a excelência em produtos e serviços, contribuindo para a satisfação do cliente e o sucesso a longo prazo.