Calibração e Qualificação de Equipamentos Essenciais
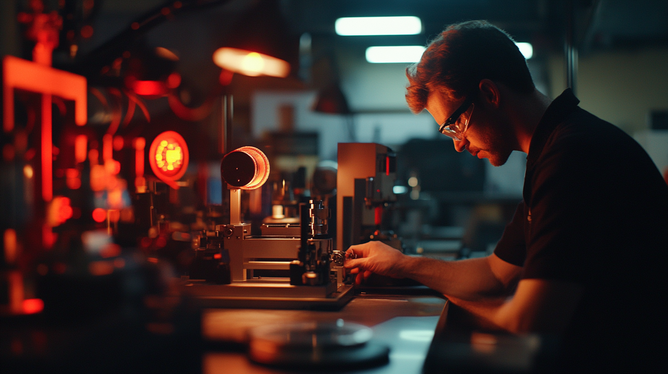
Por: Rafael - 21 de Dezembro de 2024
<p>Calibração e qualificação de equipamentos são processos fundamentais para garantir a precisão e a eficiência nas operações industriais. Neste artigo, exploraremos a importância desses procedimentos, as etapas envolvidas e os diferentes tipos de equipamentos que precisam ser qualificados. Você também descobrirá os benefícios de manter uma rotina de calibração regular, essencial para a eficácia e a segurança dos processos. Continue lendo para entender melhor como esses aspectos impactam diretamente a qualidade e a confiabilidade da sua produção.</p><h2>Importância da Calibração e Qualificação de Equipamentos</h2> <p>A calibração e a qualificação de equipamentos desempenham um papel crucial em diversos setores, especialmente na indústria e na saúde. Essas práticas garantem que os dispositivos e instrumentos utilizados nas operações estejam funcionando corretamente, proporcionando resultados precisos e confiáveis. Neste conteúdo, discutiremos em detalhes a importância desses processos, como eles impactam a qualidade dos produtos e serviços, além de abordar as consequências de não realizá-los.</p> <p>A calibração é o processo de ajustar e verificar o desempenho de um equipamento em relação a um padrão conhecido. O objetivo é garantir que os instrumentos forneçam medições precisas e consistentes. A qualificação, por sua vez, refere-se à série de testes e validações realizadas para garantir que um equipamento esteja em conformidade com as especificações de operação e que funcione adequadamente dentro do ambiente para o qual foi designado.</p> <p>Um dos benefícios mais importantes da calibração é a precisão. Equipamentos calibrados mantêm a fidelidade nas medições, o que, por sua vez, garante que os dados gerados sejam confiáveis. Isso é especialmente relevante em indústrias onde a medição precisa é vital, como na farmacêutica, alimentícia e de manufatura. Por exemplo, em laboratórios farmacêuticos, a precisão nas medições pode afetar a eficácia de um medicamento. Portanto, a calibração garante que os produtos atendam aos padrões de qualidade necessários.</p> <p>Além disso, a calibração regular ajuda a identificar possíveis falhas nos equipamentos antes que se tornem um problema maior. Ao monitorar e ajustar os dispositivos, as empresas podem evitar paradas inesperadas na produção e reduzir os custos operacionais. A manutenção proativa dos equipamentos é mais econômica do que a correção de falhas significativas e suas consequências, que podem incluir problemas de segurança e perdas financeiras.</p> <p>No setor da saúde, a calibração é igualmente essencial. Equipamentos médicos, como monitores de pressão arterial e máquinas de ultrassom, devem fornecer dados precisos para garantir o tratamento adequado dos pacientes. A falta de calibração pode levar a diagnósticos incorretos e, em última instância, a resultados adversos para a saúde dos pacientes. Portanto, a calibração de equipamentos médicos é frequentemente regulamentada e deve seguir rígidos padrões estabelecidos por órgãos regulatórios.</p> <p>Na área de qualidade, a calibração e a qualificação de equipamentos ajudam as empresas a atenderem normas e certificações, como ISO 9001 e outras regulamentações específicas do setor. Essas certificações não apenas aumentam a confiança do consumidor, mas também asseguram que os processos atendam a padrões de qualidade internacionalmente reconhecidos. As empresas que não realizam calibração e qualificação de forma regular podem enfrentar dificuldades em obter e manter essas certificações, resultando em desvantagens competitivas.</p> <p>Outro aspecto fundamental da calibração e da qualificação é a segurança. Em setores como petróleo e gás, energia e transporte, medidas de segurança rigorosas são necessárias para proteger os trabalhadores e o meio ambiente. Equipamentos não calibrados podem falhar, levando a acidentes graves, danos materiais e até exemplos de riscos à vida. Portanto, a calibragem regular não é apenas uma questão de precisão; é uma questão de segurança pública.</p> <p>Adicionalmente, a calibração e a qualificação ajudam a promover uma cultura de melhoria contínua dentro das organizações. Quando as empresas priorizam essas práticas, elas sinalizam aos seus colaboradores que a qualidade e a precisão são fundamentais para o sucesso. Isso pode levar a uma maior conscientização sobre a importância de seguir procedimentos e protocolos, o que, em última análise, se traduz em melhorias na qualidade geral do produto ou serviço.</p> <p>Os custos associados à calibração e qualificação de equipamentos são muitas vezes considerados elevados. No entanto, é vital analisar esses custos em comparação com os potenciais prejuízos causados pela falta de precisão e falhas de equipamento. Um investimento em calibração é, na verdade, uma economia a longo prazo. Ao garantir que os equipamentos estejam sempre calibrados e qualificados, as empresas podem evitar erros dispendiosos, retrabalhos e danos à reputação.</p> <p>Finalmente, vale mencionar que a tecnologia tem desempenhado um papel importante na calibração e qualificação de equipamentos. Dispositivos de medição modernos estão equipados com software avançado que facilita o monitoramento constantemente e fornece diagnósticos automáticos. Isso permite que as organizações realizem calibrações de forma mais eficiente e eficaz, reduzindo o tempo de inatividade e aumentando a precisão. Além disso, soluções em nuvem e IoT (Internet das Coisas) permitem que os dados de desempenho dos equipamentos sejam monitorados em tempo real, possibilitando intervenções imediatas quando necessário.</p> <p>Em resumo, a calibração e a qualificação de equipamentos são essenciais para manter a precisão, segurança e conformidade com os regulamentos em vários setores. Ignorar esses processos pode levar a consequências graves, incluindo falhas de equipamento, perdas financeiras, problemas de segurança e danos à reputação da empresa. Portanto, assegurar que os equipamentos sejam regularmente calibrados e qualificados é um investimento em qualidade, segurança e sucesso a longo prazo.</p> <h2>Etapas do Processo de Calibração</h2> <p>A calibração é uma prática essencial em muitos setores, garantindo que os equipamentos e instrumentos estejam operando com precisão e consistência. O processo de calibração envolve várias etapas, cada uma delas fundamental para garantir resultados confiáveis. Neste artigo, iremos detalhar as principais etapas do processo de calibração, desde a preparação até a documentação dos resultados.</p> <p>1. <strong>Identificação do Equipamento</strong></p> <p>Antes de iniciar qualquer processo de calibração, é fundamental identificar corretamente o equipamento que será calibrado. Isso inclui coletar informações detalhadas, como o modelo, número de série, especificações técnicas e procedimento de operação. Essa etapa também envolve a verificação das condições de uso do equipamento, uma vez que fatores como temperatura, umidade e vibração podem impactar os resultados durante o processo de calibração.</p> <p>2. <strong>Seleção dos Padrões de Referência</strong></p> <p>Após a identificação do equipamento, o próximo passo é selecionar os padrões de referência adequados. Os padrões de referência são instrumentos ou dispositivos calibrados contra os quais o equipamento a ser calibrado será comparado. Esses padrões devem ser rastreáveis a padrões nacionais ou internacionais, garantindo que a calibração realizada seja confiável. A escolha incorreta dos padrões de referência pode resultar em medições imprecisas e, consequentemente, afetar a qualidade do processo.</p> <p>3. <strong>Preparação do Equipamento</strong></p> <p>A calibração deve ser realizada em um ambiente controlado e adequado para garantir que fatores externos não influenciem os resultados. Isso envolve a preparação do equipamento, incluindo a limpeza e verificação da integridade do instrumento. Se o equipamento apresentar qualquer dano, ele deve ser reparado antes de prosseguir com a calibração. Também é importante que o equipamento esteja em condições de operação normal, ou seja, deve ser utilizado o mesmo equipamento sob as mesmas condições que normalmente seriam utilizadas.</p> <p>4. <strong>Realização da Calibração</strong></p> <p>Com todas as etapas de preparação concluídas, chega-se à fase de realização da calibração. Nesta etapa, o equipamento é submetido a uma série de medições comparativas utilizando os padrões de referência selecionados anteriormente. As medições devem ser realizadas em diferentes pontos de referência, conforme recomendado pelo fabricante o, por norma de calibração específica para aquele tipo de equipamento. A análise destes pontos permite identificar quaisquer desvios em relação ao padrão.</p> <p>Durante a calibração, é importante registrar todos os dados obtidos. Isso incluirá os valores medidos, os valores de referência e qualquer ajuste realizado. Esses registros são importantes tanto para a documentação quanto para a análise da performance do equipamento ao longo do tempo. Com isso, as operações podem ser rastreadas e, se necessário, ajustes podem ser feitos para otimizar o desempenho.</p> <p>5. <strong>Ajustes Necessários</strong></p> <p>Após realizar as medições, pode ser necessário ajustar o equipamento, principalmente se foram identificados desvios em relação aos padrões de referência. Os ajustes devem ser realizados conforme os procedimentos estabelecidos pelo fabricante e documentados de forma apropriada. É importante que esses ajustes sejam feitos por profissionais qualificados, para garantir que as alterações sejam corretas e não introduzam novos erros no equipamento.</p> <p>6. <strong>Documentação</strong></p> <p>A documentação é uma etapa fundamental do processo de calibração. Uma vez que a calibração foi realizada e os ajustes necessários foram efetuados, todos os resultados devem ser registrados em um documento formal de calibração. Esse relatório deve incluir detalhes como a data da calibração, identificação do equipamento, condições ambientais, valores medidos, valores de referência, ajustes feitos e a assinatura do responsável pela calibração.</p> <p>A documentação correta assegura a rastreabilidade dos equipamentos e serve como um histórico para futuras calibrações. Além disso, essa documentação é crucial em casos de auditorias e inspeções, garantindo que a empresa mantenha conformidade com normas e regulamentos aplicáveis.</p> <p>7. <strong>Verificação Pós-Calibração</strong></p> <p>Depois que a calibração e os ajustes forem finalizados, uma verificação pós-calibração deve ser realizada. Esta verificação consiste em realizar medições adicionais para garantir que os ajustes feitos estejam corretos e que o equipamento esteja agora operando conforme os padrões estabelecidos. Esse passo é importante para validar a eficácia da calibração e garantir que o equipamento está pronto para uso.</p> <p>8. <strong>Programação de Calibrações Futuras</strong></p> <p>Após o processo de calibração, é fundamental estabelecer um cronograma para futuras calibrações. Muitas empresas adotam um sistema de calibração preventiva, onde calibrações são realizadas em intervalos regulares, independentemente de verificar se o equipamento apresenta ou não falhas. O cronograma deve levar em consideração a frequência do uso do equipamento, a criticidade das medições realizadas e as recomendações do fabricante.</p> <p>9. <strong>Treinamento e Conscientização</strong></p> <p>Por último, mas não menos importante, a calibração deve ser acompanhada de um programa de treinamento e conscientização para as equipes que manuseiam os equipamentos. Treinar os usuários sobre a importância da calibração, como identificar sinais de que um equipamento pode estar fora de especificação e os procedimentos de manutenção diária ajuda a aumentar a eficiência dos processos e a vida útil dos equipamentos. Além disso, promove uma cultura de excelência operativa dentro da organização.</p> <p>10. <strong>Monitoramento Contínuo</strong></p> <p>Por fim, implementar um sistema de monitoramento contínuo pode revolucionar o processo de calibração. Ferramentas baseadas em tecnologia que coletam dados em tempo real permitem que as empresas identifiquem falhas ou desvios rapidamente. Esse monitoramento ativo pode tornar o processo de calibração mais proativo, minimizando interrupções e garantindo que os equipamentos estejam sempre dentro das especificações adequadas.</p> <p>Em resumo, o processo de calibração é essencial para garantir a precisão e a confiabilidade dos equipamentos utilizados em diversas indústrias. Seguir cada uma das etapas mencionadas, desde a identificação do equipamento até o monitoramento contínuo, contribui significativamente para a manutenção da qualidade e eficiência operacional. As empresas que investem na calibração de seus instrumentos não apenas asseguram a conformidade regulatória, mas também se colocam em uma posição competitiva mais forte no mercado, garantindo produtos e serviços de alta qualidade.</p><h2>Diferentes Tipos de Equipamentos para Qualificação</h2> <p>A qualificação de equipamentos é um processo crucial em muitas indústrias, garantindo que os dispositivos e instrumentos utilizados atendam aos padrões de qualidade e segurança necessários. Esse processo é particularmente importante em setores como farmacêutico, alimentício, de manufatura e em laboratórios. Neste artigo, exploraremos os diferentes tipos de equipamentos que podem ser qualificados e a importância de cada um deles na manutenção da qualidade dos processos e produtos.</p> <p>Antes de entrarmos nos tipos específicos de equipamentos, é importante entender que a qualificação pode ser dividida em várias categorias, dependendo do uso e das especificações do equipamento. A qualificação pode incluir a aceitação do equipamento no momento da instalação (IQ - Installation Qualification), a operação do equipamento (OQ - Operational Qualification) e o desempenho do equipamento sob condições reais de operação (PQ - Performance Qualification).</p> <p>1. <strong>Equipamentos de Medição</strong></p> <p>Os equipamentos de medição são fundamentais em praticamente todas as indústrias. Esses dispositivos são utilizados para obter medições precisas de diversos parâmetros, como temperatura, pressão, umidade, pH, entre outros. A calibração e qualificação dos equipamentos de medição são vitais, pois pequenas variações podem resultar em consequências significativas, como produtos fora de especificação e riscos à saúde do consumidor.</p> <p>Exemplos de equipamentos de medição incluem:</p> <ul> <li><strong>Termômetros</strong>: Utilizados para medir a temperatura em processos de fabricação e armazenamento.</li> <li><strong>Manômetros</strong>: Equipamentos que medem a pressão em sistemas diversos, fundamentais para se garantir que as condições operacionais estejam seguras.</li> <li><strong>Medidores de Umidade</strong>: Usados em indústrias onde a umidade pode afetar a qualidade do produto, como na indústria alimentícia e farmacêutica.</li> </ul> <p>2. <strong>Equipamentos de Processamento</strong></p> <p>Equipamentos de processamento são utilizados em diversas operações industriais, como mistura, filtração, destilação e embalagem. A qualificação desses equipamentos é crítica para garantir que os resultados obtidos estejam em conformidade com as especificações e regulamentos do setor. A inadequação ou o mau funcionamento de um equipamento de processamento pode ter um impacto significativo na qualidade do produto final.</p> <p>Alguns equipamentos de processamento que requerem qualificação incluem:</p> <ul> <li><strong>Tanques de Mistura</strong>: Usados para garantir a homogeneidade das misturas, que é essencial na produção de alimentos, cosméticos e fármacos.</li> <li><strong>Reatores Químicos</strong>: Equipamentos que promovem reações químicas; é vital que estejam operando nas condições exatas para garantir a qualidade do produto.</li> <li><strong>Máquinas de Embalagem</strong>: Garantem que os produtos sejam embalados de forma adequada, evitando contaminações e garantindo a integridade do produto até o consumidor final.</li> </ul> <p>3. <strong>Equipamentos de Laboratório</strong></p> <p>Laboratórios de pesquisa e desenvolvimento, bem como laboratórios de controle de qualidade, dependem de equipamentos altamente especializados. A qualificação desses equipamentos é essencial para garantir que os resultados dos testes e análises sejam válidos e reproduzíveis. Esses equipamentos incluem uma variedade de dispositivos que realizam medições e análises em diversas amostras.</p> <p>Alguns exemplos de equipamentos de laboratório que requerem qualificação incluem:</p> <ul> <li><strong>Espectrofotômetros</strong>: Usados para medir a absorção de luz por uma amostra, geralmente em análises químicas e bioquímicas.</li> <li><strong>Centrífugas</strong>: Utilizadas para separar componentes de uma mistura, é crucial que suas velocidades e temperaturas estejam corretas.</li> <li><strong>Incubadoras</strong>: Equipamentos que criam condições de temperatura e umidade controladas para o cultivo de microrganismos, células ou tecidos.</li> </ul> <p>4. <strong>Equipamentos de Controle de Qualidade</strong></p> <p>Os equipamentos de controle de qualidade desempenham um papel vital na manutenção da qualidade dos produtos finais. Esses dispositivos avaliam se os produtos atendem aos padrões desejados e podem incluir uma variedade de testes mecânicos, físicos e químicos.</p> <p>Exemplos de equipamentos de controle de qualidade incluem:</p> <ul> <li><strong>Máquinas de Teste de Resistência</strong>: Utilizadas para medir a resistência de materiais a tensões e pressões.</li> <li><strong>Equipamentos de Análise Química</strong>: Como cromatógrafos, que são utilizados para separar e analisar os componentes químicos de uma amostra.</li> <li><strong>Máquinas de Teste de Microbiologia</strong>: Utilizadas para detectar e quantificar microrganismos em produtos alimentícios e farmacêuticos.</li> </ul> <p>5. <strong>Equipamentos de Segurança</strong></p> <p>Os equipamentos de segurança são projetados para garantir a proteção dos trabalhadores e do ambiente. A qualificação destes equipamentos é essencial, pois falhas em equipamentos de segurança podem resultar em acidentes graves.</p> <p>Alguns equipamentos de segurança importantes incluem:</p> <ul> <li><strong>Sistemas de Alarme</strong>: Utilizados para detectar condições anormais, como vazamentos de gás ou superaquecimento.</li> <li><strong>Equipamentos de Proteção Individual (EPIs)</strong>: Sistemas que garantem a segurança do trabalhador, como máscaras e luvas, e devem ser qualificados quanto à eficácia.</li> <li><strong>Extintores de Incêndio</strong>: Precisam ser verificados para garantir que estão operacionais e dentro do prazo de validade.</li> </ul> <p>6. <strong>Equipamentos de Armazenamento</strong></p> <p>Os equipamentos de armazenamento são utilizados para manter produtos e materiais sob condições controladas. A qualificação desses equipamentos é vital para garantir que as condições de armazenamento estejam em conformidade com as exigências dos produtos, preservando sua qualidade e segurança.</p> <p>Alguns exemplos incluem:</p> <ul> <li><strong>Refrigeradores e Congeladores</strong>: Usados para armazenar produtos perecíveis, precisam ser qualificados para garantir que mantenham temperaturas adequadas.</li> <li><strong>Tanques de Armazenamento</strong>: Utilizados para armazenar líquidos, como químicos e combustíveis, devem passar por qualificação para garantir que não haja vazamentos.</li> <li><strong>Estantes e Plataformas de Armazenamento</strong>: Equipamentos que suportam cargas pesadas precisam ser verificados quanto à integridade estrutural.</li> </ul> <p>7. <strong>Equipamentos de Automação e Controles</strong></p> <p>Os sistemas de automação e controle são cada vez mais utilizados nas indústrias modernas para otimizar processos e garantir que os parâmetros operacionais estejam dentro das especificações. A qualificação desses sistemas é crucial, pois a falha nesses equipamentos pode resultar em variações indesejadas nos processos, comprometendo a qualidade do produto.</p> <p>Exemplos incluem:</p> <ul> <li><strong>Controladores de Processo</strong>: Utilizados para regular variáveis como temperatura, pressão e fluxo.</li> <li><strong>Sensores e Atuadores</strong>: Equipamentos que monitoram e controlam as condições do ambiente de produção.</li> <li><strong>Sistemas de Supervisão e Aquisição de Dados (SCADA)</strong>: São utilizados para monitorar e controlar processos industriais em tempo real.</li> </ul> <p>8. <strong>Equipamentos e Sistemas de TI</strong></p> <p>Com a crescente digitalização dos processos industriais, a qualificação de equipamentos e sistemas de TI se tornou essencial. A qualidade dos dados gerados e manipulados por softwares também precisa ser garantida, além da integridade física do hardware.</p> <p>Os equipamentos e sistemas que devem ser qualificados incluem:</p> <ul> <li><strong>Servidores e Redes</strong>: Equipamentos que armazenam e processam dados, devem estar em conformidade para evitar falhas de sistema.</li> <li><strong>Software de Gestão de Qualidade</strong>: Ferramentas que monitoram e rastreiam a qualidade dos produtos, exigem validação para garantir que gerem relatórios precisos.</li> <li><strong>Dispositivos de Backup e Recuperação de Dados</strong>: Equipamentos que armazenam informações cruciais devem ser verificados regularmente para garantir a segurança da informação.</li> </ul> <p>9. <strong>Considerações Finais</strong></p> <p>A qualificação de diversos tipos de equipamentos é um componente essencial para garantir que os processos industriais e de laboratório funcionem de maneira eficaz e eficiente. A identificação correta dos equipamentos que precisam de qualificação, juntamente com a realização de calibrações regulares, proporciona segurança, qualidade e conformidade com os regulamentos do setor. A execução metódica das etapas de qualificação, a seleção das tecnologias adequadas e o treinamento do pessoal não são apenas recomendações, mas sim requisitos essenciais para garantir a operação bem-sucedida e segura em qualquer ambiente produtivo.</p> <p>Em uma era onde a qualidade é cada vez mais exigida pelo mercado e pelos consumidores, investir na qualificação de equipamentos não é apenas uma boa prática; é uma necessidade fundamental. A aplicação dessas técnicas não apenas protege as empresas contra riscos de não conformidade, mas também ajuda a construir uma reputação sólida e confiável no mercado. Portanto, garantir que cada tipo de equipamento esteja qualificado é vital para o sucesso e a sustentabilidade das operações em várias indústrias.</p> <h2>Benefícios da Calibração Regular em Indústrias</h2> <p>A calibração regular é uma prática essencial em diversas indústrias, assegurando que equipamentos e instrumentos operem com precisão e eficiência. Essa prática não apenas contribui para a qualidade dos produtos finais, mas também para a segurança dos processos e a conformidade com normas regulatórias. Neste artigo, examinaremos os principais benefícios da calibração regular em indústrias e como essa estratégia pode impactar positivamente a operação e a reputação de uma empresa.</p> <p>1. <strong>Precisão nas Medições</strong></p> <p>Um dos benefícios mais evidentes da calibração regular é a precisão nas medições. Equipamentos calibrados garantem que os dados gerados sejam confiáveis, o que é crucial em setores como farmacêutico, alimentício e de manufatura, onde mesmo pequenas variações podem resultar em produtos fora das especificações.</p> <p>Quando um equipamento não está calibrado, as medições podem ser imprecisas e levar a decisões erradas, como a interrupção da produção ou, pior ainda, a comercialização de um produto defeituoso. Ao realizar calibrações regulares, as empresas podem ter confiança nos resultados, minimizando assim o risco de erros dispendiosos.</p> <p>2. <strong>Redução de Custos</strong></p> <p>A calibração regular também ajuda a reduzir custos operacionais. Equipamentos que não são calibrados frequentemente podem acabar apresentando problemas de funcionamento, o que leva a quebras inesperadas e custos elevados de reparo. Além disso, a produção pode ser interrompida, resultando em perdas financeiras significativas.</p> <p>Ao adotar uma abordagem proativa e implementar um cronograma de calibração, as indústrias podem evitar esses problemas, garantindo que os equipamentos operem em condições ideais. Isso não só reduz os custos de manutenção, mas também aumenta a vida útil dos maquinários, proporcionando economia a longo prazo.</p> <p>3. <strong>Conformidade Regulamentar</strong></p> <p>Muitas indústrias estão sujeitas a regulamentos rigorosos e padrões de qualidade que exigem a calibração regular de equipamentos. A falta de conformidade pode resultar em penalidades severas, ações legais e danos à reputação da empresa. Certificações como ISO 9001, por exemplo, requerem um rigoroso sistema de manutenção e calibração.</p> <p>Portanto, manter um cronograma regular de calibração assegura que a empresa não apenas atenda às exigências legais, mas também demonstre comprometimento com a qualidade e segurança. Isso pode resultar em uma reputação mais forte e em maiores oportunidades de negócios.</p> <p>4. <strong>Manutenção da Qualidade do Produto</strong></p> <p>Quando se trata de produção, manter a qualidade do produto é de suma importância. A calibração regular dos equipamentos assegura que os produtos atendam às especificações exigidas e que estejam livres de erros. Um produto bem calibado contribui para a sua aceitação no mercado e para a satisfação do cliente.</p> <p>Se um instrumento de medição estiver desatualizado, por exemplo, os produtos podem não atingir os padrões desejados, levando a desperdícios, retornos e reclamações. A calibração frequente ajuda a garantir que esses problemas sejam evitados, resultando em uma produção mais eficiente e em crescimento nas vendas.</p> <p>5. <strong>Aumento da Segurança</strong></p> <p>Uma calibração regular dos equipamentos também impacta diretamente na segurança do ambiente de trabalho. Equipamentos que estão fora de calibração podem apresentar falhas, que podem resultar em acidentes, ferimentos ou até pior. Por exemplo, em indústrias onde são manipuladas substâncias químicas perigosas, a precisão na medição de pressão e temperatura é crítica para evitar explosões ou vazamentos.</p> <p>Ao garantir que todos os equipamentos estejam calibrados e funcionando corretamente, as indústrias não apenas protegem seus funcionários, mas também evitam perdas financeiras e danos à reputação decorrentes de incidentes de segurança.</p> <p>6. <strong>Aumento da Eficiência Operacional</strong></p> <p>Outro benefício significativo da calibração regular é o aumento da eficiência operacional. Equipamentos devidamente calibrados tendem a operar de maneira mais suave e eficiente, eliminando desperdícios e melhorando a produtividade. Quando os instrumentos de medição e controle estão funcionando corretamente, as operações podem ser otimizadas, resultando em um uso mais eficaz dos recursos.</p> <p>Além disso, a calibração regular permite que os operadores identifiquem e corrijam problemas antes que se transformem em interrupções, aumentando ainda mais a eficiência. Uma operação eficiente se traduz em uma maior capacidade de atender às demandas dos clientes e de lucrar com melhores margens de produção.</p> <p>7. <strong>Documentação e Rastreabilidade</strong></p> <p>Realizar calibrações regulares implica em manter uma documentação detalhada de todos os procedimentos e resultados. Isso não só ajuda a rastrear a performance do equipamento ao longo do tempo, mas também facilita auditorias e inspeções. Documentar os resultados de calibração é uma consideração importante para indústrias que precisam se manter em conformidade com regulamentações e padrões da indústria.</p> <p>A documentação também permite que as empresas analisem tendências e desenvolvam estratégias para melhorar ainda mais a eficiência e a eficácia da produção. É um elemento fundamental que pode ser utilizado para justificar investimentos em novos equipamentos ou melhorias de processo.</p> <p>8. <strong>Melhoria Contínua</strong></p> <p>Implementar um regime de calibração regular incentiva uma cultura de melhoria contínua dentro da organização. À medida que os departamentos adotam práticas sistemáticas de manutenção e calibração, os colaboradores se tornam mais conscientizados sobre a importância da qualidade e da conformidade. Isso pode levar à identificação de áreas onde melhorias podem ser feitas, resultando em processos mais eficientes e aprimoramento na qualidade do produto.</p> <p>Equipamentos que são tratados como parte integrante do processo produtivo geram um ciclo de feedback positivo, onde os colaboradores se incentivam a buscar sempre métodos mais eficientes e melhores práticas.</p> <p>9. <strong>Fortalecimento da Confiança do Cliente</strong></p> <p>A calibração regular não apenas melhora a qualidade e a segurança dos produtos, mas também ajuda a construir uma relação de confiança com os clientes. Quando uma empresa demonstra um comprometimento genuíno com a qualidade e a segurança, ela se destaca no mercado e atrai clientes que estão dispostos a pagar mais por produtos confiáveis.</p> <p>Além disso, a qualidade consistente dos produtos aumenta a probabilidade de fidelização do cliente e promove recomendações positivas, fortalecendo ainda mais a posição da empresa no mercado.</p> <p>10. <strong>Aumento da Competitividade</strong></p> <p>A calibração regular é um diferencial competitivo em um mercado cada vez mais exigente. Empresas que investem em manutenção de qualidade não apenas atendem às expectativas, mas frequentemente superam a concorrência. A capacidade de oferecer produtos de qualidade superior, juntamente com a eficiência nos processos, posiciona a empresa como uma líder no setor.</p> <p>Além disso, empresas com uma boa reputação em qualidade e segurança têm a capacidade de expandir suas operações e alcançar novos mercados, uma vez que consumidores e parceiros de negócios preferem trabalhar com prestadores de serviços confiáveis e com compromisso com a excelência.</p> <p>Em conclusão, a calibração regular de equipamentos é essencial para garantir a precisão, segurança e eficiência nas operações industriais. Os benefícios são evidentes em várias dimensões, abrangendo a redução de custos, a satisfação do cliente e a conformidade com regulamentos. Ao se comprometer com uma prática sistemática de calibração, as indústrias não apenas asseguram a qualidade de seus produtos e processos, mas também se posicionam para um futuro sustentável e competitivo.</p> <p>Em suma, a calibração e a qualificação de equipamentos desempenham um papel crucial na manutenção da qualidade e segurança nos processos industriais. À medida que discutimos a importância dessas práticas, as etapas necessárias e os diferentes tipos de equipamentos envolvidos, fica evidente que a calibração regular não é apenas uma formalidade, mas uma necessidade indispensável para empresas que visam excelência e competitividade. Através da implementação de rotinas de calibração e qualificação, as indústrias podem garantir medições precisas, reduzir custos, aumentar a eficiência operacional e fortalecer a confiança do cliente. Portanto, investir em calibração é investir no futuro, assegurando não apenas a conformidade com normas regulatórias, mas também a sustentabilidade e o sucesso a longo prazo de quaisquer operações. As práticas de calibração e qualificação efetivamente estabelecem o alicerce para a qualidade, segurança e confiabilidade que o mercado exige, tornando-as uma prioridade para qualquer organização comprometida em se destacar em seu setor.</p>