Calibração e Aferição de Instrumentos de Medição: Garantindo Precisão e Confiabilidade
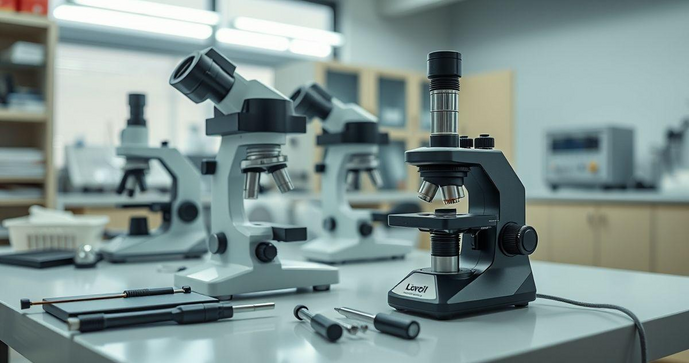
Por: Rafael - 21 de Março de 2025
<p>A calibração e aferição de instrumentos de medição são processos fundamentais para garantir a precisão e a confiabilidade dos resultados em diversas aplicações industriais e laboratoriais. Esses procedimentos asseguram que os instrumentos estejam funcionando corretamente, evitando erros que podem comprometer a qualidade dos produtos e serviços. Neste artigo, abordaremos a importância da calibração e aferição, os métodos utilizados, a frequência recomendada para esses processos e os erros comuns que devem ser evitados.</p><h2>Importância da Calibração e Aferição na Indústria</h2><p>A calibração e aferição de instrumentos de medição são processos cruciais na indústria, pois garantem que os equipamentos utilizados estejam operando com precisão e confiabilidade. Esses procedimentos são essenciais para manter a qualidade dos produtos, a segurança dos processos e a conformidade com normas e regulamentos. A seguir, discutiremos em detalhes a importância da calibração e aferição na indústria, abordando seus impactos em diferentes setores.</p><p>Um dos principais motivos para realizar a calibração e aferição é a necessidade de garantir a precisão das medições. Em ambientes industriais, instrumentos de medição, como medidores de pressão, temperatura e vazão, são utilizados para monitorar e controlar processos. Se esses instrumentos não estiverem calibrados corretamente, as medições podem estar erradas, levando a decisões inadequadas que podem afetar a qualidade do produto final. Por exemplo, um <a href="https://www.flowmetercalibra.com.br/medidor-vazao-agua-ultrassonico" data-inner-link="Medidor de vazão ultrassônico">Medidor de vazão ultrassônico</a> que não está calibrado pode resultar em medições imprecisas, causando desperdício de recursos e aumento de custos operacionais.</p><p>Além disso, a calibração e aferição são fundamentais para a segurança dos processos industriais. Em setores como o químico e o petroquímico, onde substâncias perigosas são manipuladas, a precisão nas medições é vital para evitar acidentes. Um instrumento de medição que falha pode resultar em vazamentos, explosões ou contaminações, colocando em risco a vida dos trabalhadores e o meio ambiente. Portanto, a calibração regular desses instrumentos é uma prática essencial para garantir a segurança operacional.</p><p>Outro aspecto importante é a conformidade com normas e regulamentos. Muitas indústrias são obrigadas a seguir padrões específicos de qualidade e segurança, que incluem a calibração e aferição de instrumentos de medição. Organizações como a ISO (Organização Internacional de Normalização) estabelecem diretrizes que as empresas devem seguir para garantir a qualidade de seus produtos e serviços. A não conformidade pode resultar em penalidades, perda de certificações e danos à reputação da empresa. Portanto, a calibração e aferição não são apenas boas práticas, mas também requisitos legais em muitos casos.</p><p>A calibração e aferição também desempenham um papel importante na eficiência operacional. Quando os instrumentos de medição estão funcionando corretamente, os processos industriais podem ser otimizados, resultando em maior produtividade e redução de custos. Por exemplo, um sistema de controle de temperatura que opera com precisão pode garantir que os processos de aquecimento e resfriamento sejam realizados de forma eficiente, evitando desperdícios de energia e recursos. Isso não apenas melhora a eficiência, mas também contribui para a sustentabilidade das operações industriais.</p><p>Além disso, a calibração e aferição ajudam a prolongar a vida útil dos equipamentos. Instrumentos de medição que não são calibrados regularmente podem sofrer desgastes e danos, resultando em falhas e necessidade de substituição. Ao realizar a calibração e aferição de forma sistemática, as empresas podem identificar problemas potenciais antes que se tornem críticos, economizando tempo e dinheiro com manutenções corretivas e substituições de equipamentos.</p><p>Outro ponto a ser considerado é a confiança dos clientes. Em um mercado competitivo, a qualidade dos produtos e serviços é um diferencial importante. Quando uma empresa demonstra compromisso com a calibração e aferição de seus instrumentos de medição, ela transmite confiança aos seus clientes, que podem ter certeza de que estão recebendo produtos de alta qualidade. Isso pode resultar em maior satisfação do cliente, fidelização e, consequentemente, aumento nas vendas.</p><p>Por fim, a calibração e aferição de instrumentos de medição são essenciais para a inovação e desenvolvimento de novos produtos. Em ambientes de pesquisa e desenvolvimento, a precisão nas medições é fundamental para garantir que os resultados sejam confiáveis e reproduzíveis. Isso é especialmente importante em setores como farmacêutico e alimentício, onde a pesquisa e desenvolvimento de novos produtos exigem medições precisas para garantir a eficácia e segurança dos produtos finais.</p><p>Em resumo, a calibração e aferição de instrumentos de medição são práticas indispensáveis na indústria. Elas garantem a precisão das medições, a segurança dos processos, a conformidade com normas e regulamentos, a eficiência operacional, a prolongação da vida útil dos equipamentos, a confiança dos clientes e a inovação. Portanto, investir em calibração e aferição é um passo fundamental para qualquer empresa que busca manter a qualidade e a competitividade no mercado.</p><h2>Métodos Comuns de Calibração e Aferição</h2><p>A calibração e aferição de instrumentos de medição são processos essenciais para garantir a precisão e a confiabilidade dos resultados em diversas aplicações industriais e laboratoriais. Existem vários métodos utilizados para realizar esses procedimentos, cada um com suas características e adequações a diferentes tipos de instrumentos. Neste artigo, abordaremos os métodos mais comuns de calibração e aferição, destacando suas vantagens e aplicações.</p><p>Um dos métodos mais tradicionais de calibração é a calibração por comparação. Neste método, o instrumento a ser calibrado é comparado a um padrão de referência conhecido e rastreável. O padrão de referência pode ser um instrumento de medição que já foi calibrado e possui um certificado de calibração. Durante o processo, as medições do instrumento em teste são comparadas com as do padrão, e as discrepâncias são registradas. Esse método é amplamente utilizado em laboratórios e indústrias, pois permite identificar rapidamente desvios e ajustar o instrumento conforme necessário.</p><p>Outro método comum é a calibração em ponto fixo. Este método envolve a calibração do instrumento em um ou mais pontos específicos de medição. Por exemplo, um termômetro pode ser calibrado em pontos de temperatura conhecidos, como 0°C e 100°C, para garantir que suas medições estejam corretas nessas temperaturas. A calibração em ponto fixo é especialmente útil para instrumentos que operam em faixas de medição limitadas, pois permite uma verificação precisa em pontos críticos. No entanto, é importante notar que esse método pode não detectar desvios em outras partes da faixa de medição.</p><p>A calibração em múltiplos pontos é uma extensão do método de calibração em ponto fixo. Neste caso, o instrumento é calibrado em vários pontos ao longo de sua faixa de medição. Isso proporciona uma visão mais abrangente do desempenho do instrumento e permite identificar desvios em diferentes condições de operação. A calibração em múltiplos pontos é especialmente recomendada para instrumentos que serão utilizados em uma ampla gama de condições, garantindo que a precisão seja mantida em toda a faixa de operação.</p><p>Além dos métodos mencionados, a calibração por simulação é outra técnica utilizada, especialmente em instrumentos eletrônicos. Neste método, um sinal elétrico conhecido é aplicado ao instrumento, e a resposta do instrumento é medida. Isso é particularmente útil para instrumentos que não podem ser calibrados diretamente, como medidores de vazão ultrassônicos. A calibração por simulação permite verificar se o instrumento responde corretamente a diferentes condições de entrada, garantindo que ele funcione conforme o esperado em situações reais.</p><p>A aferição, por sua vez, é um processo que envolve a verificação da precisão de um instrumento de medição em relação a um padrão de referência. A aferição pode ser realizada de forma semelhante à calibração, mas geralmente é menos formal e pode não envolver ajustes no instrumento. A aferição é frequentemente utilizada em ambientes onde a precisão é crítica, mas onde ajustes não são necessários ou desejáveis. Por exemplo, em uma linha de produção, um instrumento pode ser aferido regularmente para garantir que suas medições estejam dentro de limites aceitáveis, sem a necessidade de recalibração frequente.</p><p>Outro método importante é a calibração por transferência. Este método é utilizado quando não é possível realizar a calibração diretamente no instrumento em questão. Em vez disso, um instrumento de referência é utilizado para calibrar um segundo instrumento em um ambiente diferente. Isso é comum em situações em que o instrumento a ser calibrado está em um local remoto ou em operação contínua. A calibração por transferência permite que as empresas mantenham a precisão de seus instrumentos sem a necessidade de interromper a operação.</p><p>É importante ressaltar que a escolha do método de calibração e aferição deve levar em consideração o tipo de instrumento, a faixa de medição, a precisão necessária e as condições de operação. Além disso, muitas empresas optam por contratar <a href="https://www.flowmetercalibra.com.br/empresas-calibracao-equipamentos" data-inner-link="Empresas de calibração de equipamentos">empresas de calibração de equipamentos</a> especializadas para garantir que os procedimentos sejam realizados de acordo com as normas e padrões estabelecidos. Essas empresas possuem conhecimento técnico e equipamentos adequados para realizar calibrações precisas e confiáveis.</p><p>Por fim, a documentação é um aspecto crucial em qualquer processo de calibração e aferição. É fundamental registrar todos os resultados, ajustes realizados e condições de teste. Isso não apenas garante a rastreabilidade dos instrumentos, mas também fornece um histórico que pode ser útil para auditorias e conformidade com normas regulatórias. A documentação adequada é uma parte essencial do processo, pois ajuda a manter a qualidade e a confiabilidade dos instrumentos de medição ao longo do tempo.</p><p>Em resumo, os métodos de calibração e aferição são variados e devem ser escolhidos com base nas necessidades específicas de cada instrumento e aplicação. A calibração por comparação, em ponto fixo, em múltiplos pontos, por simulação e a aferição são algumas das técnicas mais comuns utilizadas na indústria. A escolha do método adequado, juntamente com a contratação de empresas especializadas, garante que os instrumentos de medição operem com precisão e confiabilidade, contribuindo para a qualidade e segurança dos processos industriais.</p><h2>Frequência Recomendada para Calibração e Aferição</h2><p>A calibração e aferição de instrumentos de medição são processos essenciais para garantir a precisão e a confiabilidade dos resultados em diversas aplicações industriais e laboratoriais. No entanto, a eficácia desses processos depende não apenas da execução correta, mas também da frequência com que são realizados. A seguir, discutiremos a frequência recomendada para calibração e aferição, considerando diferentes fatores que podem influenciar essa periodicidade.</p><p>Um dos principais fatores a ser considerado ao determinar a frequência de calibração e aferição é o tipo de instrumento utilizado. Instrumentos que operam em condições extremas, como altas temperaturas, pressões elevadas ou ambientes corrosivos, tendem a exigir calibrações mais frequentes. Por exemplo, um <a href="https://www.flowmetercalibra.com.br/venda-medidores-vazao" data-inner-link="Medidor de vazão">Medidor de vazão</a> que é utilizado em um ambiente industrial agressivo pode sofrer desgastes mais rapidamente, o que pode afetar sua precisão. Portanto, é recomendável que esses instrumentos sejam calibrados com maior frequência, como a cada três meses ou até mensalmente, dependendo das condições de operação.</p><p>Outro fator importante a ser considerado é a frequência de uso do instrumento. Instrumentos que são utilizados com alta frequência, como aqueles em linhas de produção, podem exigir calibrações mais regulares. O uso constante pode levar a desgastes e variações nas medições, tornando essencial a realização de calibrações periódicas para garantir a precisão. Em geral, para instrumentos de uso intensivo, uma calibração mensal ou trimestral pode ser adequada, enquanto instrumentos utilizados ocasionalmente podem ser calibrados semestralmente ou anualmente.</p><p>A natureza do processo em que o instrumento está inserido também influencia a frequência de calibração. Em setores onde a precisão é crítica, como na indústria farmacêutica ou alimentícia, a calibração deve ser realizada com mais frequência. Nesses setores, a conformidade com normas rigorosas de qualidade e segurança é fundamental, e a calibração regular é uma parte essencial para garantir que os produtos atendam aos padrões exigidos. Assim, a calibração pode ser realizada mensalmente ou até semanalmente, dependendo da criticidade do processo.</p><p>Além disso, a estabilidade do instrumento ao longo do tempo deve ser considerada. Alguns instrumentos podem apresentar variações de desempenho ao longo do tempo, enquanto outros mantêm sua precisão por períodos mais longos. É importante monitorar o desempenho do instrumento e ajustar a frequência de calibração conforme necessário. Se um instrumento começar a apresentar desvios frequentes, pode ser um sinal de que a calibração deve ser realizada com mais regularidade.</p><p>Outro aspecto a ser considerado é a recomendação do fabricante. Muitos fabricantes de instrumentos de medição fornecem diretrizes específicas sobre a frequência de calibração e aferição. Essas recomendações são baseadas em testes e análises realizadas pelo fabricante e devem ser seguidas para garantir o desempenho ideal do instrumento. Ignorar essas diretrizes pode resultar em medições imprecisas e comprometer a qualidade dos processos.</p><p>Além disso, a realização de auditorias internas e externas pode influenciar a frequência de calibração. Muitas empresas optam por realizar auditorias regulares para garantir a conformidade com normas e regulamentos. Durante essas auditorias, a calibração e aferição dos instrumentos de medição são frequentemente verificadas. Se uma empresa estiver sujeita a auditorias frequentes, pode ser necessário aumentar a frequência de calibração para garantir que todos os instrumentos estejam em conformidade.</p><p>É importante também considerar a documentação e o histórico de calibração do instrumento. Manter registros detalhados das calibrações realizadas, incluindo datas, resultados e ajustes feitos, pode ajudar a identificar padrões e determinar a frequência ideal de calibração. Se um instrumento apresentar resultados consistentes e precisos ao longo do tempo, pode ser possível estender o intervalo entre as calibrações. Por outro lado, se um instrumento apresentar variações frequentes, pode ser necessário aumentar a frequência de calibração.</p><p>Por fim, a cultura organizacional e a conscientização sobre a importância da calibração e aferição também desempenham um papel na frequência com que esses processos são realizados. Empresas que valorizam a qualidade e a precisão tendem a realizar calibrações com mais regularidade, enquanto aquelas que não priorizam esses aspectos podem negligenciar a calibração. Promover uma cultura de qualidade e conscientização sobre a importância da calibração pode levar a uma maior frequência de calibração e, consequentemente, a melhores resultados.</p><p>Em resumo, a frequência recomendada para calibração e aferição de instrumentos de medição varia de acordo com diversos fatores, incluindo o tipo de instrumento, a frequência de uso, a natureza do processo, a estabilidade do instrumento, as recomendações do fabricante, auditorias e a documentação do histórico de calibração. É fundamental que as empresas avaliem esses fatores e estabeleçam uma programação de calibração que atenda às suas necessidades específicas, garantindo a precisão e a confiabilidade dos instrumentos de medição ao longo do tempo.</p><h2>Erros Comuns na Calibração e Como Evitá-los</h2><p>A calibração de instrumentos de medição é um processo crítico que garante a precisão e a confiabilidade das medições em diversas aplicações industriais e laboratoriais. No entanto, erros podem ocorrer durante esse processo, comprometendo a eficácia da calibração e, consequentemente, a qualidade dos resultados obtidos. Neste artigo, abordaremos os erros comuns na calibração e como evitá-los, garantindo que os instrumentos de medição operem de maneira eficiente e precisa.</p><p>Um dos erros mais frequentes na calibração é a falta de um padrão de referência adequado. A calibração deve ser realizada em comparação com um padrão que seja rastreável e reconhecido. Se o padrão utilizado não for confiável ou não estiver devidamente calibrado, as medições do instrumento em teste também estarão comprometidas. Para evitar esse erro, é fundamental utilizar padrões de referência que sejam calibrados por uma <a href="https://www.flowmetercalibra.com.br/empresas-calibracao-instrumentos-medicao-sp" data-inner-link="Empresa de calibração de instrumentos de medição">empresa de calibração de instrumentos de medição</a> reconhecida e que possuam certificados de rastreabilidade. Isso garante que as medições sejam precisas e confiáveis.</p><p>Outro erro comum é a falta de condições ambientais controladas durante o processo de calibração. Fatores como temperatura, umidade e vibração podem afetar o desempenho dos instrumentos de medição. Por exemplo, um termômetro calibrado em um ambiente com temperaturas extremas pode apresentar resultados imprecisos. Para evitar esse problema, é importante realizar a calibração em um ambiente controlado, onde as condições sejam mantidas dentro dos limites especificados pelo fabricante do instrumento. Isso ajuda a garantir que os resultados da calibração sejam representativos das condições reais de operação.</p><p>A falta de treinamento adequado dos profissionais responsáveis pela calibração também é um erro que pode comprometer a precisão do processo. A calibração requer conhecimento técnico e habilidades específicas para garantir que os procedimentos sejam seguidos corretamente. Profissionais não treinados podem cometer erros ao realizar medições, ajustes ou interpretações dos resultados. Para evitar esse problema, as empresas devem investir em treinamento contínuo para suas equipes, garantindo que todos os envolvidos no processo de calibração estejam atualizados sobre as melhores práticas e procedimentos.</p><p>Além disso, a falta de documentação adequada é um erro que pode levar a problemas na calibração. É fundamental manter registros detalhados de todas as calibrações realizadas, incluindo datas, resultados, ajustes e condições de teste. A documentação não apenas garante a rastreabilidade, mas também fornece um histórico que pode ser útil para auditorias e conformidade com normas regulatórias. Para evitar a falta de documentação, as empresas devem implementar um sistema de gerenciamento de calibração que facilite o registro e o acompanhamento das calibrações realizadas.</p><p>Outro erro comum é a calibração em pontos inadequados. A calibração deve ser realizada em pontos que representem a faixa de operação do instrumento. Se a calibração for feita apenas em um ou dois pontos, pode não ser possível identificar desvios em outras partes da faixa de medição. Para evitar esse problema, é recomendável realizar a calibração em múltiplos pontos ao longo da faixa de operação do instrumento. Isso proporciona uma visão mais abrangente do desempenho do instrumento e ajuda a garantir que a precisão seja mantida em toda a faixa de operação.</p><p>A negligência na verificação de ajustes após a calibração também é um erro que pode comprometer os resultados. Após a calibração, é importante verificar se o instrumento está funcionando corretamente e se os ajustes realizados foram eficazes. Ignorar essa etapa pode resultar em medições imprecisas e comprometer a qualidade dos processos. Para evitar esse problema, as empresas devem implementar procedimentos de verificação pós-calibração, garantindo que todos os instrumentos sejam testados e validados após a calibração.</p><p>Além disso, a falta de manutenção regular dos instrumentos de medição pode levar a erros na calibração. Instrumentos que não são mantidos adequadamente podem apresentar desgastes e falhas, afetando sua precisão. Para evitar esse problema, as empresas devem estabelecer um programa de manutenção preventiva que inclua inspeções regulares e manutenção dos instrumentos. Isso ajuda a garantir que os instrumentos estejam sempre em boas condições de funcionamento e prontos para a calibração.</p><p>Por fim, a resistência a mudanças e a falta de atualização dos procedimentos de calibração também podem ser um erro comum. À medida que novas tecnologias e métodos de calibração são desenvolvidos, é importante que as empresas estejam dispostas a revisar e atualizar seus procedimentos. Ignorar inovações pode resultar em processos obsoletos e ineficientes. Para evitar esse problema, as empresas devem promover uma cultura de melhoria contínua, incentivando a adoção de novas práticas e tecnologias que possam aprimorar a calibração e a aferição de instrumentos de medição.</p><p>Em resumo, os erros comuns na calibração podem comprometer a precisão e a confiabilidade dos instrumentos de medição. A falta de padrões de referência adequados, condições ambientais controladas, treinamento adequado, documentação, calibração em pontos inadequados, verificação pós-calibração, manutenção regular e resistência a mudanças são alguns dos principais erros a serem evitados. Ao implementar boas práticas e procedimentos adequados, as empresas podem garantir que seus instrumentos de medição operem com precisão e confiabilidade, contribuindo para a qualidade e segurança dos processos industriais.</p><p>Em conclusão, a calibração e aferição de instrumentos de medição são essenciais para a manutenção da qualidade e segurança em ambientes industriais e laboratoriais. Através da compreensão da importância desses processos, da aplicação de métodos adequados, da definição de frequências apropriadas e da identificação de erros comuns, as empresas podem garantir que seus instrumentos operem com precisão e confiabilidade. Investir em calibração e aferição não apenas melhora a eficiência operacional, mas também fortalece a confiança dos clientes e a conformidade com normas regulatórias. Portanto, é fundamental que as organizações adotem práticas rigorosas de calibração e aferição, assegurando a excelência em seus processos e produtos.</p>